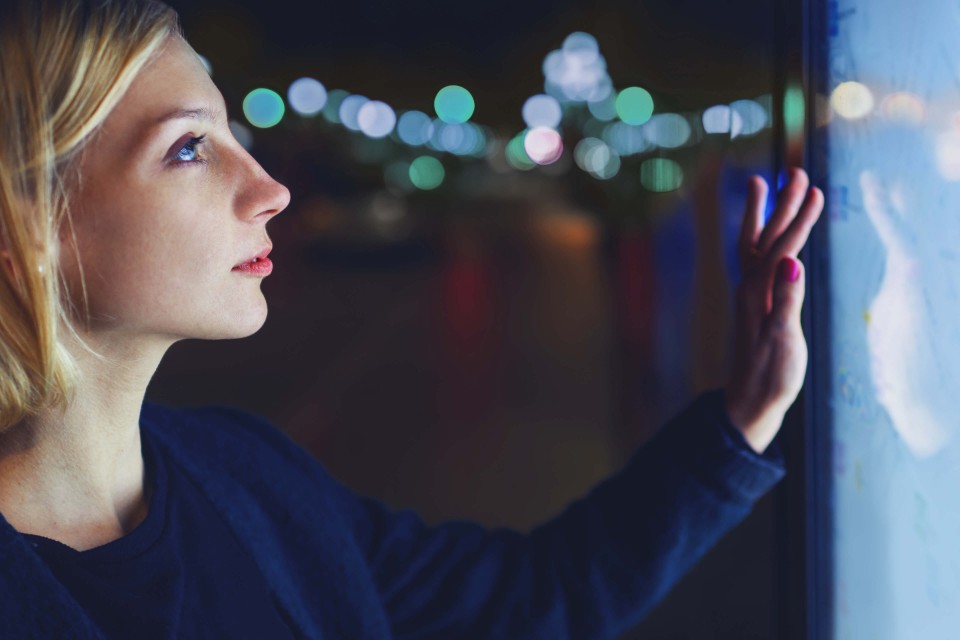
Powerful material with great potential
Oct 01, 2019 Read time: approx. MinutesMinute
Smart silicone sandwiches
Thanks to their electroactive properties, laminates that comprise electrodes and ultrathin silicone films can measure movement. They can also be made to expand and contract on demand. In the future, WACKER will be producing such prefabricated electronics components for sensors and actuators that will only require customers to fit the necessary electrical connections.
They adjust headlamps, position side mirrors correctly and regulate the radio volume: in cars, some 300 actuators carry out a wide range of functions – from the drive train to the central locking system. The units convert electrical pulses into movement. Actuators play a key role not just in automotive engineering, but in robotics, electrical engineering and medical technology, too. Novel varieties based on electroactive polymers, in particular, are gaining in popularity in these sectors due to their positive properties.
In its ultrathin high-precision silicone film – already available on the market as ELASTOSIL® Film since 2013 – WACKER has created a powerful material with great potential. “We are now transforming this technology into specific products and are thus making it more readily available for the market,” says Renate Glowacki, who is responsible for the worldwide marketing of the silicone films at WACKER SILICONES’ Global Business Development.
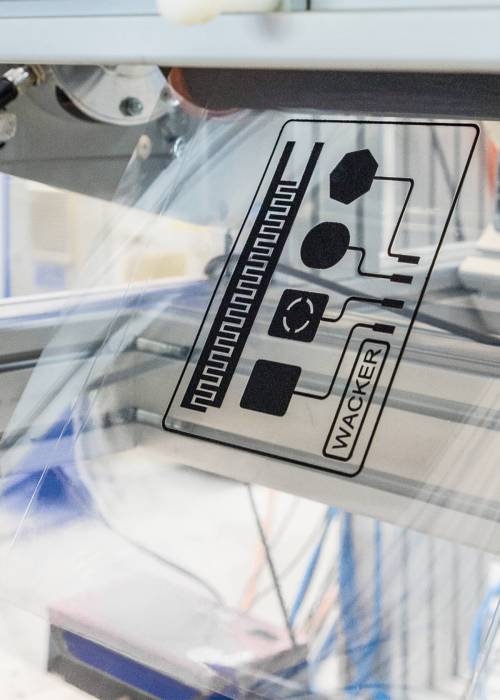
WACKER production plant for NEXIPAL® laminates. Electrode printing is flexible, so it can be tailored to individual customer needs.
Vertical integration
By manufacturing laminates, WACKER is implementing vertical integration and is thus moving one step further along the supply chain toward industrial application. An exhibit that was developed in collaboration with the University of Saarland will allow visitors of the K 2019 plastics tradeshow (October 16 to 23 in Düsseldorf) to try out the laminates’ sensor-actuator functions themselves.

On account of their dielectric properties, silicone elastomers are categorized as electroactive polymers (EAPs). “When there is a single thin film embedded between each pair of electrodes, you get a laminate – layers bonded together on top of each other,” says Dr. Andreas Köllnberger, who played a key role in the development of these silicone films at WACKER. If an electric voltage is applied to this sandwich, a flexible capacitor is created. “Due to their opposite charges, the electrodes attract each other electrostatically and deform the silicone film between them, making it thinner, but at the same time longer and wider,” reports the WACKER chemist. “Its volume thus stays the same.” Overall, the capacitor ends up thinner, but also larger in area. When the capacitor is discharged, the elasticity of the laminate causes it to return to its original shape.
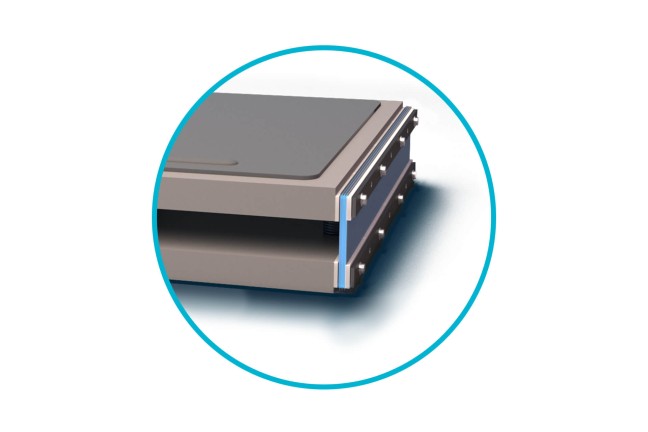
Once the laminate is formed, the end user sees only the flat display, which rises and falls or begins to vibrate whenever pressure is applied to the appropriate areas. As a result, the display gives users the impression that they can actually feel the virtual keys.
The entire process is silent and can be repeated millions of times. “Since this deformation can be selectively controlled, these EAP laminates – marketed under the NEXIPAL® trademark – are suitable as actuators that convert electric voltage into mechanical movement. Conversely, EAP laminates can use mechanical movement – such as finger pressure – to produce changes in capacitance, and can thus be used as sensors. Even novel generators are possible,” adds Dr. Johannes Neuwirth, who is a technical design expert and responsible for forward integration at WACKER SILICONES’ Global Business Development unit.
At K 2019, WACKER is presenting an exhibit that illustrates the combination of sensor and actuator: a smartphone mounted on a structure with EAP elements. They cause the phone to vibrate slightly at high frequency , as the fingers, gliding over the display surface, touch certain areas. This gives the impression of a rippled surface or even keys, which are not really there.
The benefits of EAP laminates
The exhibit not only demonstrates the function of the laminates and the integrated electroactive polymers, it also reveals the potential of such haptic feedback for various applications. Motorists, for instance, can find controls in the center console more easily by touch – entirely without eye contact. What is more, the actuator elements make for greater freedom of design. In other words, it is possible to create designs that are thinner or narrower than solenoid valves. Freedom of design extends to the surfaces too – in this particular case, the buttons. They can be designed to be angular or circular or given any other shape, the actual design being determined by the algorithm underlying a particular program.
EAP actuators made of silicone laminates are compact and thus save space. They require up to 30 percent less space and are up to 40 percent lighter than conventional components, depending on configuration and design. The energy needs of EAP actuators are also low. They require less than 10 percent of the overall electrical energy needed by conventional actuators. Hence, EAP actuators are extremely energy-efficient and sustainable. This and their silent mode of action make the innovative laminate an ideal component not only in electric vehicles.
WACKER manufactures high-precision silicone films that are between 20 and 400 micrometers thick, with the thickness deviating by less than five percent over the entire width. This homogeneity is crucial for a uniform electric field, which is necessary to ensure that the NEXIPAL® laminates will later function optimally and reliably.
The high-precision films are made entirely of addition-curing silicone rubber. To exclude contamination, they are produced in cleanrooms. Like all silicone rubber compounds, the films are heat- and UV-resistant, flexible at low temperatures and chemically inert. Additionally, they are extremely elastic and do not wear out. “Our tests show that ELASTOSIL® Film can survive over ten million load cycles without displaying fatigue,” emphasizes Dr. Köllnberger.
First there was silicone film, then NEXIPAL®
When WACKER started producing silicone films in 2013, it, in a way, entered unchartered territory. Until then, the chemical company had confined itself to bringing silicone rubber compounds onto the market as uncured raw materials.
In the case of silicone films, however, many customers quickly wanted the option of obtaining a processed semi-finished product – an EAP laminate. That’s why the Group decided to close this gap in the processing chain itself.
By now, WACKER experts have extensively familiarized themselves with the technical requirements demanded of EAP components, for example by mechatronic systems, and built up a wealth of relevant expertise. A production plant for EAP laminates is currently under construction. These are prefabricated EAP components that will only require customers to fit the necessary electrical connection. The first of these components, which will be marketed under the NEXIPAL® brand, are expected to roll off the production line in mid-2020.
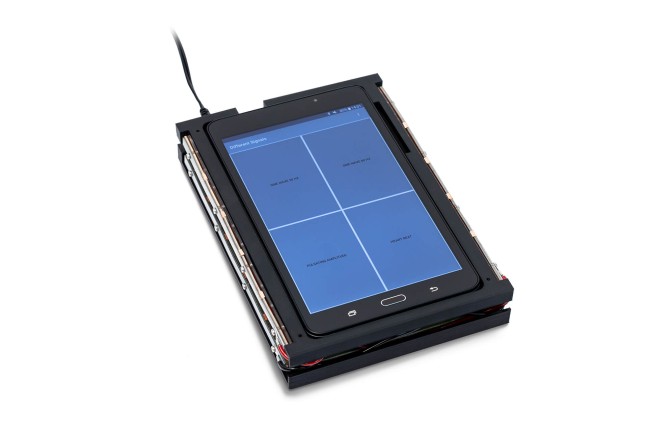
You can use a smartphone fitted with electroactive polymer laminates almost without having to look at it. The various applications can be felt – even though the surface of the display remains “smooth”.
In the manufacture of these laminates, the existing silicone film will be coated with a special conductive material, which serves as the electrode. The new plant will be able to produce several of these layers. The size and shape of the laminate are flexible, and customer-specific electrode designs can be ordered, too.
EAP components can also be produced as strips. Customers can subsequently transform these into rolled actuators, for example.
“Several challenges had to be overcome in developing the production process,” reports Dr. Neuwirth. For example, there must be no air trapped between the individual layers of an EAP sandwich. “The handling of the ultrathin films in the coating process was a complex undertaking, too,” he continues. The extent to which EAP actuators can contract, and the displacement they undergo in the process, depend on several factors. The driving voltage that is applied to the EAP component plays a key role here. For this reason, the silicone films must be as thin as possible.
“The thinner the film, the lower the applied voltage necessary to achieve the desired movement effect. That’s why we are working on further reducing the film thickness.”
Dr. Andreas Köllnberger, WACKER chemist
Intelligent design
The use of high-quality electrodes and an intelligent EAP component design can also reduce the required voltage. Another option for reducing the voltage is to increase the permittivity of silicone films, for instance by doping them with special particles. In addition, a spring design can be used to produce components that achieve considerable displacement.
Alongside the advantages already mentioned, EAP actuators offer a further benefit: they can be used as artificial muscles that, unlike solenoid valves, can execute fluid, i.e. flowing movements.
This property makes silicone laminates interesting not only for the automotive and electronics industries, but also in medical technology, sensor technology and robotics. The silicone sandwiches even find use in printed electronics.
“Whether as a component of biomimetic robots, portable medical technology or instruments for human-machine communication: electroactive silicone laminates are conceivable in many promising applications.”
Renate Glowacki, Global Business Development Manager at WACKER SILICONES

Production process for NEXIPAL® EAP laminates
How an actuator and sensor comprising NEXIPAL® laminate works
The electroactive properties of silicone film laminates mean they can be used as actuators or sensors. Actuators are drive system components that convert an electrical signal emitted by control electronics into mechanical movement. Sensors work along similar lines. Capacitive sensors measure mechanical movements.
A voltage source is applied to the NEXIPAL® laminate, which comprises at least one ultrathin film and at least two electrodes, to ensure the laminate can operate as an actuator.
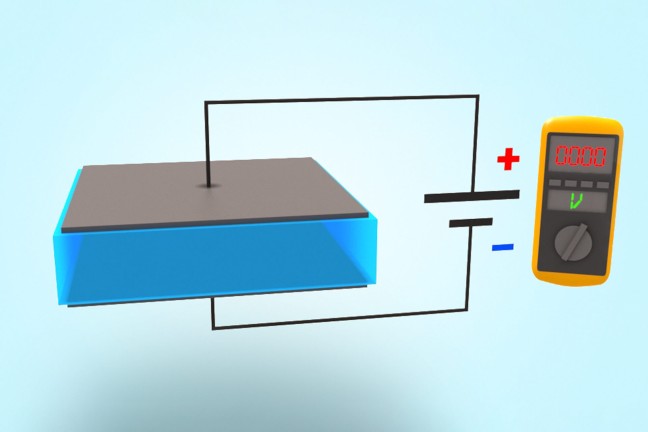
Turning on a voltage source charges one electrode positively and the other negatively. The electrodes attract one another and deform the silicone film. This makes the film thinner, yet wider so that the volume stays the same. The actuator moves. If the voltage is turned off, the silicone film returns to its original state, thereby pushing the electrodes apart again.
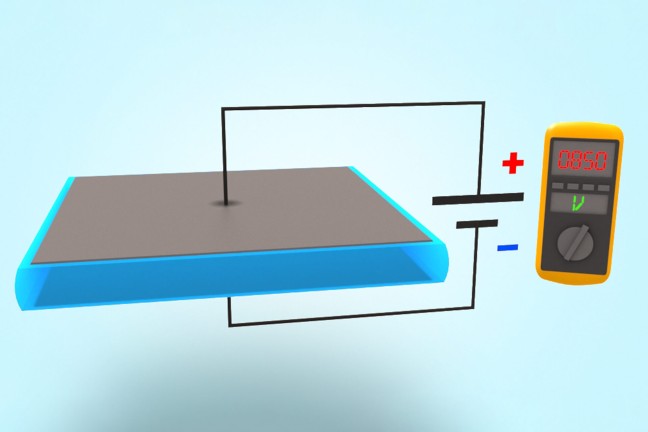
An EAP sensor works along similar lines. A measuring instrument is connected to the NEXIPAL® laminate to measure the capacitance.
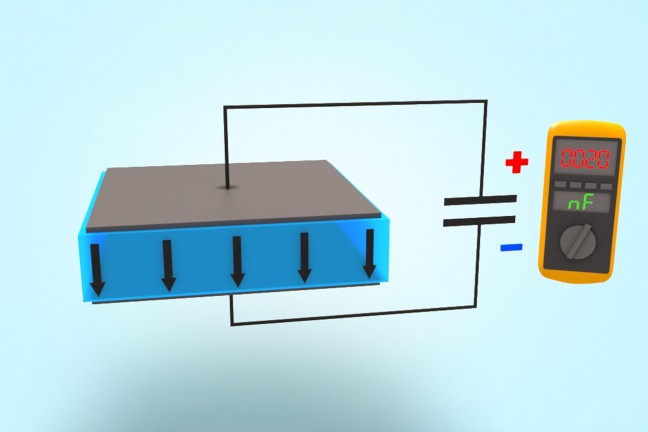
The NEXIPAL® laminate can then be deformed by compressive or tensile movements. The electrostatic field between the electrodes changes depending on how far apart the electrodes are.
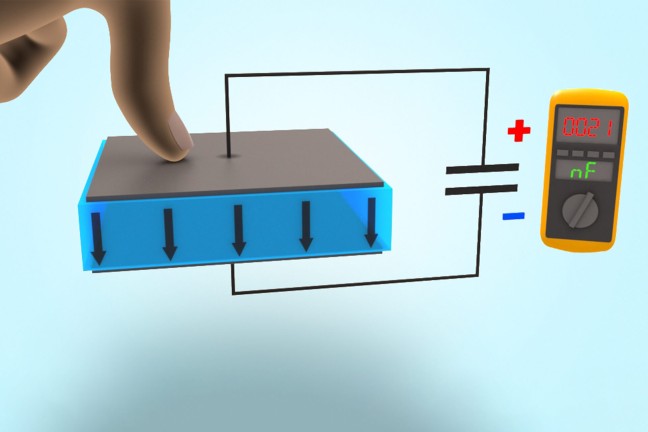
Since hardly any force is needed to deform the silicone film, it is enough to apply a slight pressure with your finger to bring the electrodes closer together. The distance between them changes and so does the capacitance, which is shown on the instrument. As soon as you remove your finger, the silicone film pushes the electrodes back into their original state.
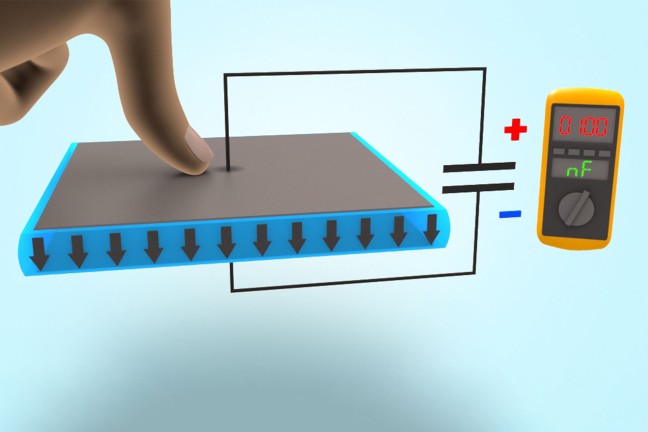
Contact
For more information on this topic, please contact:
Mrs. Renate Glowacki
Business Development Manager
Engineering Silicones
+49 89 6279-1813
nexipal@wacker.com