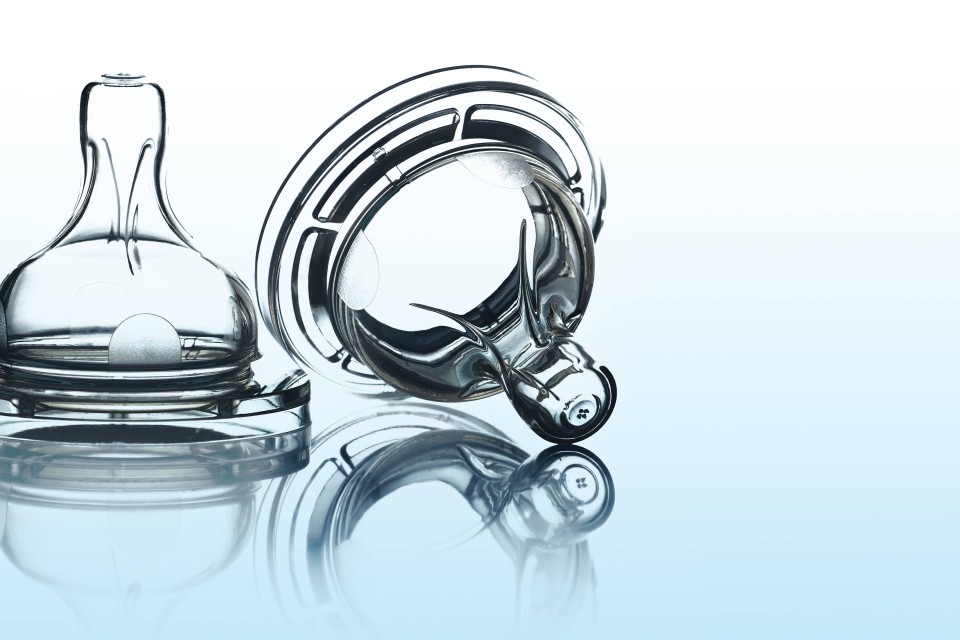
Quickly, efficiently, cost-effectively and very precisely
Oct 01, 2019 Read time: approx. MinutesMinute
Setting new standards
Up to now, silicone products often required postcuring to achieve the desired properties. But help is now on the way, because WACKER has considerably reduced the residual volatile substances in its liquid silicone rubber products.
Liquid silicone rubber – which professionals also refer to by its acronym LSR – has become firmly established on the market since it was introduced in the 1980s. “A key reason why is because you can use a fully automated injection-molding process to turn silicones like these into molded silicone parts,” explains Dr. Thomas Frese, who runs an applications lab for the Rubber Solutions business team within WACKER SILICONES. “That allows us to produce parts in large quantities – quickly, efficiently, cost-effectively and very precisely.”
In most cases, the molded parts are postcured. Examples of when this downstream heat treatment is required include silicone objects made from conventional liquid silicones and intended for use in food, babycare or medical applications. The treatment removes any residual volatiles or extractable substances from the elastomer. This is the only way of meeting the strict regulatory requirements for silicone items used in these sensitive applications. The industry is also increasing pressure on silicone compounders to reduce the content of volatiles in finished products. As a result, silicone manufacturers are receiving increasingly frequent requests for low-volatile LSRs – for liquid silicone rubber grades, in other words, that contain very low levels of volatile substances.
Volatiles content reduced
“We rose to the challenge and significantly reduced the volatiles content of the LSR grades we manufacture in Europe,” explains Dr. Wolfgang Schattenmann, who heads up the Rubber Solutions business team at WACKER SILICONES. “In the process, we upgraded our LSR line to a low-volatile product portfolio.”
The company is also int roducing ELASTOSIL® LR 5040, a product line especially for manufacturing silicone goods for the food, babycare, pharmaceuticals and medical industries. “This product line in turn goes well beyond the new standard that our low-volatile LSR product portfolio sets,” explains Claudia Berghammer, senior marketing manager at WACKER SILICONES. “Molded parts made from ELASTOSIL® LR 5040 meet the legal requirements for sensitive applications with no need for postcuring.” The company had already unveiled this product line at K 2016, and now a broad customer base has access to the full spectrum of grades in the series.
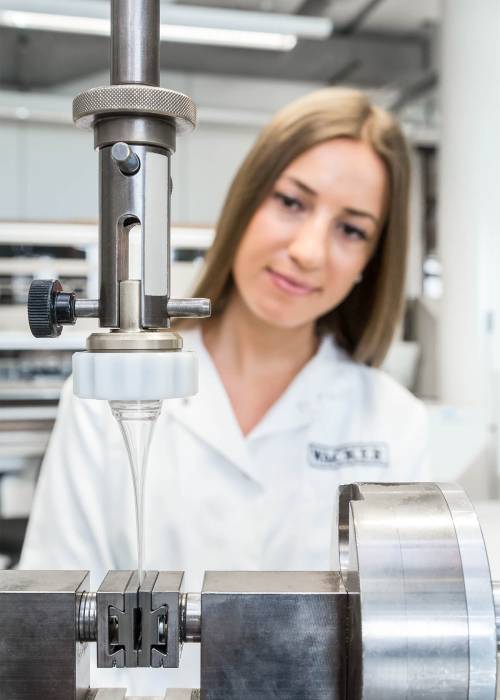
Putting the mechanical strength of cured liquid silicone rubber to the test at an applications laboratory in Burghausen; the image shows a baby bottle nipple undergoing a bite test.
“ELASTOSIL® LR 5040 completely eliminates all of the usual postcuring work so that we can gear our production directly toward final packaging.”
Martin Rapperstorfer, head of sales, RICO GROUP GmbH
In an ideal scenario, injection-molded silicone parts are ready for use without any further processing. In practice, though, it is often expedient and usually even necessary to bake out parts at high temperatures for several hours in a well-ventilated oven. The benefits of this thermal treatment step, which is known as postcuring, include improved mechanical properties of the elastomer. In addition, however, it ensures the removal of volatile components, which form as a manufacturing byproduct of the raw materials used and which are not incorporated into the elastomer network when the rubber is cured later on. Low-molecular-weight siloxanes account for the bulk of these volatile components.

VOLATILES CONTENT*: The volatiles content of non-postcured items made of ELASTOSIL® LR 5040 (blue bars) is below 0.2 to 0.3 percent, far below the threshold of 0.5 percent required for food applications by agencies such as the German Institute for Risk Assessment (BfR). A standard commercial liquid silicone, by contrast, has a volatiles content in the range of 1 to 1.2 percent prior to postcuring and, as a result, has to be postcured to stay below the threshold. (* in weight percent)

Extractable substances from standard non-postcured lsr before and after being upgraded as a low-volatiles portfolio (in ppm*): Thanks to its low-volatiles initiative, WACKER has reduced the volatiles content of its entire liquid silicone rubber portfolio by over 90 percent. Heptane extracts were prepared from cured rubber that had not undergone postcuring and were analyzed via gas chromatography to demonstrate the reduction in volatile components. (* Extractable Dx siloxanes from a heptane extract of ELASTOSIL® LR 3003/60, GC analysis)
Strict safety standards
Whether thermal post-treatment is necessary depends on the composition of the silicone rubber compound and on the intended use of the molded part. Imposing strict purity criteria is one way that legislators have set high safety standards for products intended for sensitive applications. Silicone products for food and babycare applications must be especially pure – the content of volatiles in these cases must not exceed 0.5 percent.
This is the threshold identified in the following recommendations: “XV. Silicone” from the German Federal Institute for Risk Assessment (BfR), France’s “Arrêté du 25 novembre 1992,” and the Swiss Ordinance No. 817.023.21 on Food-Contact Materials and Articles. European Standard EN 14350-2 applies to silicone products used in cups and bottles for infants and toddlers, while EN 1400 must be met for pacifiers.
As a measure of volatiles content, these regulations specify the weight that silicone objects lose when subjected to a precisely defined heat treatment – often for four hours at 200 degrees Celsius. Dried samples of molded parts must not lose more than 0.5 percent of their mass when treated in this way. Cured products of commercial liquid silicone rubber must be postcured in order to comply with these regulations.
Volatile silicone components are often undesirable in silicones used for technical applications as well. “The focus in these cases is on the effects that low-molecular-weight siloxanes can have,” says Dr. Frese. As the WACKER chemist explains, “They can spread from the silicone to other media or other objects in a number of different ways – evaporation, extraction or migration – and cause unwanted effects there. That’s why a lot of industries, including the automotive industry, are really interested in silicone rubber compounds that contain very little in the way of residual low-molecular-weight components – even though these particular regulations differ from those for sensitive applications.”
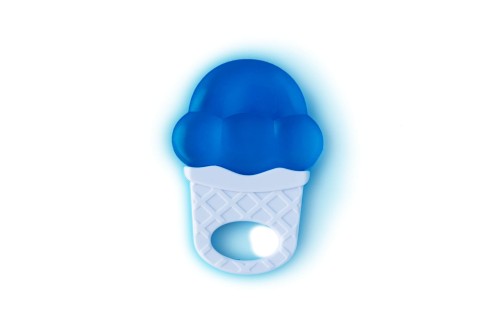
Babies’ teething ring made of ELASTOSIL® LR 5040: tear strength plays a key role in such applications.
Unique requirements
WACKER takes an approach that accounts for these different needs: on the one hand, the company has turned its entire line of LSR products into a low-volatiles portfolio; on the other, it has launched a product line on the market that is specially tailored to the unique requirements of the food, babycare, medical technology and pharmaceuticals sectors – the ELASTOSIL® LR 5040 series.
For silicone compounders, postcuring constitutes an additional processing step that not only entails considerable energy consumption and generates emissions – it also restricts productivity. Whereas injection molding and product packaging are fully automated processes with quick cycle times, postcuring is performed largely by hand. Subsequent thermal treatment interrupts the process chain and limits production capacity. Plus, if the postcuring process is not carried out correctly, explosive mixtures can form in the oven.

Tear strength(N/mm)
The tear strength of cured ELASTOSIL® LR 5040 rubber without postcuring (blue curve) is significantly higher than that of standard postcured liquid silicone rubber (red curve). That is why injection-molded parts made from ELASTOSIL® LR 5040 do not require thermal post-treatment to improve their mechanical properties prior to shipping.
This is why WACKER aimed to take this highly involved process off of silicone compounders’ hands. A team headed by Dr. Frese developed ELASTOSIL® LR 5040 specifically for sensitive applications. Using a novel, proprietary WACKER process technology and a new formulation concept as their starting point, the scientists were able to develop ELASTOSIL® LR 5040, a product line within the LSR portfolio with by far the lowest concentration of components that are volatile, extractable or capable of migrating into other materials – the products also comply with regulations governing the content of volatile substances in sensitive applications.
In addition, silicone items made from these rubber grades exhibit the excellent mechanical properties needed – even without postcuring. The postcuring process will no longer be necessary in these applications in the future.
From the perspective of a compounder like the RICO Group, an international full-service provider of customized polymer solutions, the material combines several benefits that ultimately translate into savings for customers.
“Right now, every kilo of liquid silicone rubber we process into finished parts has to be put in drums or on trays and taken over to the postcuring ovens,” says Sales Manager Martin Rapperstorfer, an engineer from Austria. “This is followed by packaging – a process in which the LSR parts have to be staged yet again. ELASTOSIL® LR 5040 completely eliminates all of that postcuring work so that we can gear our production directly toward final packaging,” he points out. “Not only does that reduce the number of work sequences involved – it also saves valuable resources in the form of energy and personnel costs.” Plus, he adds, it virtually eliminates the risk of contamination during manual steps.
The developers and technical managers on Dr. Frese’s team at WACKER also took a careful look at the various degrees of hardness available within the new ELASTOSIL® LR 5040 series. Their work revolved around the question of whether the cured rubber would meet ambitious goals in terms of workability, purity and mechanical properties.
Suitable for injection molding
Their studies show that the liquid silicones cure very rapidly and can readily be used in injection-molding processes. Hardness levels between 30 and 70 Shore A are available, including a 45 Shore A grade suitable for numerous applications in the babycare sector. The hardness values specified here refer to materials that have not undergone postcuring – which is not the case for conventional silicone rubber. And with ELASTOSIL® LR 5040, these values fall within a very narrow tolerance of ±3 Shore A points, allowing compounders to respond to their customers’ hardness requirements with exceptional precision.
The volatiles content was checked by determining the weight loss as recommended for food applications by the German Institute for Risk Assessment – a process that involved experiments with non-postcured test pieces two millimeters thick. The team performed additional studies to assess the impact of differences in geometry, and found that the weight loss was between 0.15 and 0.4 percent for all of the grades in the new product line – decidedly below the 0.5 percent hurdle. The margin of safety between these results and the threshold is so large, in other words, that legal requirements can be met in most cases without postcuring, regardless of component geometry. The scale of the weight loss was similar when samples were tested according to other European standards as well.
For silicones used in sensitive applications, there are also numerous laws and standards that specify extraction and migration limits. The corresponding requirements can be found in regulations such as CFR 21 § 177.2600 of the US Food and Drug Administration (FDA), in Section 3.1.9 of the European Pharmacopoeia, in BfR Recommendation “XV. Silicone” and in the laws of several other EU member states. ELASTOSIL® LR 5040 in its non-postcured state complies with these requirements, too. Furthermore, the non-postcured rubber products of the new liquid silicones are biocompatible as per the specifications of United States Pharmacopeia (USP) Class VI and ISO 10993.
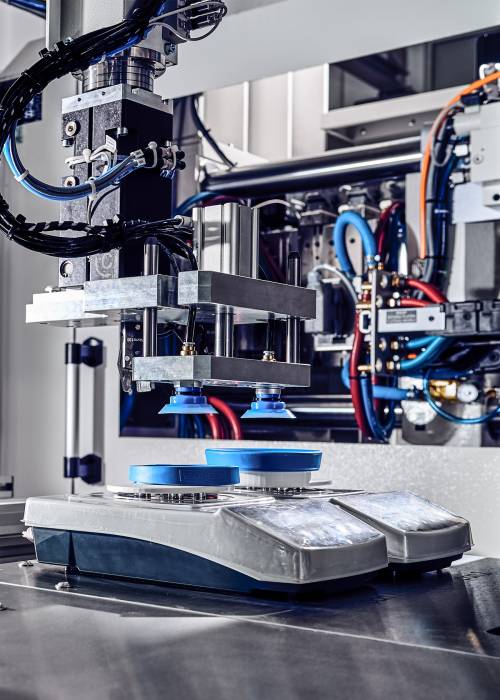
Among the things on display at the WACKER booth during this year’s K plastics tradeshow will be this injection-molding machine from ACH, a leading manufacturer of silicone-processing equipment and molds. The image shows how ELASTOSIL® LR 5040 is used to produce lids for portable and reusable coffee cups.
Pure and tear resistant
A key reason that the new liquid silicones can claim to be especially pure is their optical appearance: they are translucent and have a pale blue sheen. The resultant molded parts create an impression of particularly high quality and purity. Furthermore, the tendency to yellow, which often occurs with postcured liquid silicone articles in storage, has been reduced to a minimum.
In many sensitive applications, the demands are high with regard to not just purity, but also the mechanical properties. “The only way to achieve the necessary bite resistance in pacifiers, teething rings, nipples for baby bottles and other babycare items is to use a highly tear-resistant material,” explains Marketing Manager Claudia Berghammer. “Small cracks should not propagate when the elastomer is stretched. This is another area where our innovative silicone rubber grades perform well,” she adds. The tear resistance of her cured rubber products extends up to 50 Newtons per millimeter, measured as directed in ASTM D 624 B – even without postcuring. Cured rubber made from conventional liquid silicones does not usually achieve values like these until postcuring occurs, and then only in the cases of products specially designed to be highly tear resistant.
For the new silicone grades, WACKER has established narrow tolerances for weight loss and tests each batch to make sure it lies within these limits. Because cured rubber made from these liquid silicones – even without postcuring – falls far below the legal thresholds for volatility, extraction and migration, their use offers a great deal of safety. Whereas silicone compounders used to have to make sure that their products comply with legal limit values, ELASTOSIL® LR 5040 shifts that responsibility to a certain degree onto WACKER – relieving compounders of an appreciable burden.
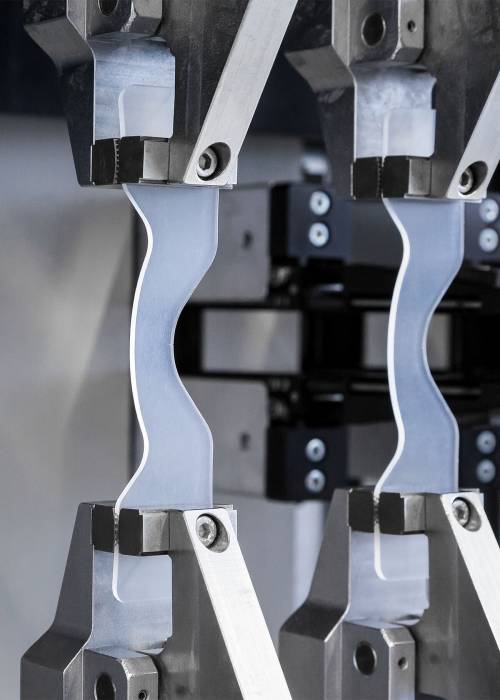
Examining the tear strength of ELASTOSIL® LR 5040 test pieces in an applications laboratory.
100 out of 100 pass the test
The developers on Thomas Frese’s team refused to be satisfied with that, however. They also wanted to know how the new silicone behaves in various babycare applications. To do this, they subjected injection-molded baby-bottle nipples made of ELASTOSIL® LR 5040 to a simulated bite test as described in EN 14350-1. The first step was to make small cuts in the nipples in a defined manner, after which the nipples were stretched and had to withstand a tensile force of 9.5 kilograms. All 100 of the nipples tested have to pass this sophisticated mechanical test – no nipple can tear prematurely.
Non-postcured bottle nipples made from the new 45 or 50 Shore A silicone fared particularly well in these tests. Even though the geometries of the nipples varied, none of them failed. The results are thus comparable, and in some cases superior, to those for postcured bottle nipples made from commercial LSR rubber compounds.
“ELASTOSIL® LR 5040 is setting a new standard thanks to its exceptionally low content of residual volatiles and to the outstanding technical properties that its cured products exhibit – even without postcuring. The products in this series define the technological frontier and have already proven themselves to be the market’s benchmark for sensitive applications.”
Dr. Wolfgang Schattenmann, director of Rubber Solutions, WACKER SILICONES
New processing possibilities
ELASTOSIL® LR 5040 opens up new possibilities for silicone compounders. The elimination of the postcuring step allows component manufacturers to streamline production and boost productivity substantially paving the way for a lean, fully automated production process that can take place entirely inside a cleanroom if need be. And because omitting the postcuring step also completely obviates the risk of explosive air mixtures, these silicones help make the production process safer.
In addition to babycare products, typical examples of silicone items that can now be made without postcuring include those that come into contact with food and those used in medical and pharmaceutical technologies – from seals for kitchen appliances, coffee makers and storage containers to metering valves and respirators.
Demand for silicone products in which the content of volatile, extractable components is as low as possible is growing in areas beyond the food, babycare and medical technology sectors, however, and applies to parts used in technical applications as well. In response, the Munich chemical company has likewise removed the volatiles from most of its liquid silicone rubber products. Significantly reducing the residual content of volatile siloxanes has greatly enhanced the value of the company’s product portfolio. Its low-volatiles initiative was concluded in early 2019 and impacts all of the LSR grades that WACKER produces in Europe, specifically its ELASTOSIL® LR 3xxx and LR 6xxx and SILPURAN® 6xxx products.
The company was able to reduce the volatiles content through process engineering optimization. This upgrade revolved around specific volatile, low-molecular-weight silicone components known as Dx siloxanes, for which there exist maximum limits in some sectors, such as the automotive industry.
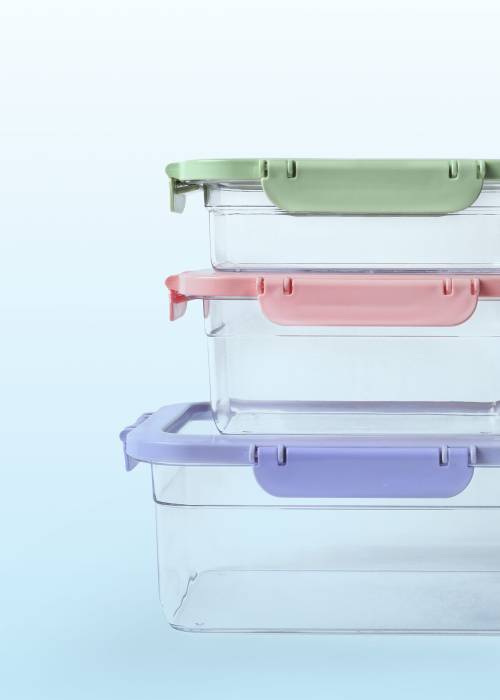
Food storage containers: an ELASTOSIL® LR 5040 silicone seal has been fitted into the organic rubber lid.
Entire lsr portfolio upgraded
This means that the volatiles content in WACKER’s new, upgraded LSR portfolio is so low that silicone compounders can meet government and industry-specific regulations more easily and with greater certainty than before. And, in some cases, compounders can actually dispense with postcuring altogether. The automotive industry is a good example here: a benchmark known as the Toyota standard defines 350 ppm as the maximum allowable amount of certain volatile Dx siloxanes2 used for connector seals or single-wire seals made of oil-bleeding silicones. Thanks to WACKER’s low-volatiles initiative, oil-bleeding products in the ELASTOSIL® LR 384x series meet this exacting standard set by Japanese automakers, even without postcuring.
According to Dr. Frese, the following issue is important for silicone compounders as well: “Upgrading the LSR portfolio has absolutely no impact on the mechanical and chemical properties of the elastomer,” he emphasizes. “Product approvals and certificates are all just as valid as they ever were.” Reducing the volatiles content also represents major progress when it comes to sustainability, he feels, because the low-molecular-weight siloxanes that are removed from these products are fed back into the production cycle, which protects the environment and preserves resources.
“The silicone rubber grades in this product line define the technological frontier on the market.”
Dr. Wolfgang Schattenmann, director of Rubber Solutions, WACKER SILICONES
Postcuring
In the materials sciences, the term “postcuring” generally refers to a heat treatment that provides this material with its end properties. This also applies to silicones. Postcured silicone parts are superior to their non-postcured counterparts, both in terms of their engineering properties and biocompatibility. In the case of cured products of addition-curing silicone rubber compounds – a category that includes liquid silicone rubber – postcuring degrades excess crosslinker, improves filler bonding and drives out low-molecular-weight silicone components. This results in a modest increase in hardness, a significant improvement in tear strength, low compression set and a reduction in the volatiles content. The established standard method is to postcure silicone pieces for four hours at 200 °C in an oven especially designed for this purpose. For safety reasons, the rate of air flow is held continuously high. Since the entire volume of air that flows through the oven has to be heated to 200 °C, postcuring consumes a great deal of energy.
Mr. Dr. Thomas Frese
Head of Technical Marketing for Rubber Solutions
WACKER SILICONES
+49 8677 83-4947
thomas.frese@wacker.com