
Innovations That Defined Decades
Nov 24, 2023 Read time: approx. MinutesMinute
Innovating Together for 60 Years: ARDEX and WACKER
Two companies with traditional roots in Germany, operating throughout the world, shaped by the same values and sharing a common success story: ARDEX and WACKER
Tile adhesives, adhesives for floorings made of wood and other materials, self-leveling flooring compounds, grout mortars, waterproofing materials – when reconstruction began gathering momentum in Germany during the post-war years, demand for building materials was high. Established in Witten as a family-owned business in 1949 (initially under a different name), ARDEX and its portfolio of chemical construction materials played a key role in helping Germany rebuild. The company quickly expanded its offerings and continued to develop its various formulations. Suppliers for the basic materials that ARDEX used in its finished products included WACKER.

While the first documented contact between ARDEX and WACKER came in the form of a series of technical experiments performed together in 1958, the first commercial shipment of WACKER dispersible polymer powders to ARDEX was delivered in 1963, marking the beginning of their common success story: in 2023, the two venerable companies celebrated 60 years of doing business together.
“Meeting the constantly changing demands of the construction industry has meant deepening our partnership with WACKER over the years. We’ve bundled our knowledge and resources, collaborating on the development of innovative, high-quality products and solutions for the construction industry and setting first-in-class standards of quality and sustainability,” says ARDEX CTO Dr. Hubert Motzet, describing their work together.
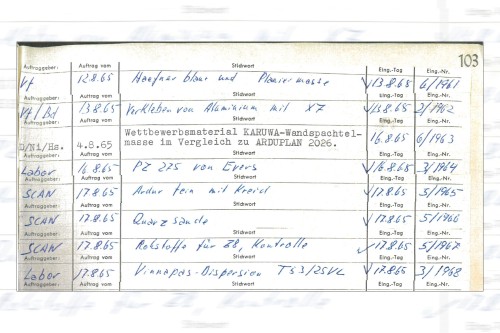
A 1965 ARDEX lab order for a shipment of VINNAPAS® – early documentary evidence of the company's many years of collaboration with WACKER.
Meeting the constantly changing demands of the construction industry has meant deepening our partnership with WACKER over the years.
Dr. Hubert Motzet, CTO of ARDEX

Innovations That Defined Decades
One sign of the companies’ joint innovative strength that has remained highly visible to this day are the architecturally spectacular facilities built for the 1972 Olympics in Munich. At one point during construction, workers had to repair a load-bearing column that had developed holes and cracks. A specialist from ARDEX did the job using a cement-based concrete filler known as Arducret B12 – an ARDEX product that, at that time, had only been available for a few months. The product contained a dispersible polymer powder made from vinyl acetate-ethylene (VAE) copolymer, which WACKER had likewise only recently begun producing. VAE copolymers in the mortar act as a second flexible binder in addition to the rigid cement, improving both the cohesion and flexibility of this unique mortar. Polymer modification also reduces the amount of water needed for the filler, which, in turn, reduces shrinkage. Thanks to these improved properties, the filler was able to repair defects in the concrete permanently. ARDEX had defined these “like-to-have” criteria in its product development, which motivated WACKER to develop a corresponding additive. Sold under the name ARDEX B 12 – Concrete Filler, the final product has now been used reliably for smoothing and leveling concrete surfaces for over 50 years.
“Like ARDEX, WACKER has been shaped by its exceptional quality awareness and by the value it places on its employees’ expertise. Together we have continuously improved our technical expertise, building on the foundation of our shared values, which include accountability, respect and solidarity. And that is what’s driven our product innovation and business success,” explains Peter Summo, head of WACKER POLYMERS.
Like ARDEX, WACKER has been shaped by its exceptional quality awareness and by the value it places on its employees’ expertise.
Peter Summo, head of WACKER POLYMERS
Laying Tiles: Thin-Bed Method Replaces the Thick-Bed Method
Alongside cement-based concrete filler Arducret B1, another product made its prominent debut at the Olympics: Ardurit X7G tile adhesive. Up to that point, the thick-bed technique was used for tiling all over the world: tiles were laid in a layer of mortar at least 1.5 centimeters thick and consisting almost exclusively of cement, sand and water. Ardurit X7G – a product we would now refer to as a flexible adhesive – made thin-bed technology an option for laying tiles in the early 1970s. “The tile adhesive,” reports Dr. Peter Fritze from Technical Service for the Construction Polymers business unit of WACKER POLYMERS, “contained a high concentration of VAE copolymers. In combination with cellulose ethers, these polymers improved tile adhesion on the substrate and helped dissipate any stress that might arise. For the first time, this meant that experts could process cementitious materials into layers less than a half centimeter thick.” Thin-bed technology – today’s standard – was born. The technology meant that tilers could cover much larger areas in the same amount of time, which was a huge advantage, given rising labor costs. Plus, the rise of densely sintered porcelain stoneware tiles and their reduced porosity – and hence greater resistance to freezing – made polymer-containing tile adhesives like Ardurit X7G a necessity. Because they would have very quickly detached from the floor or wall, there would have been no way to lay these tiles with the mortar used in the old thick-bed method.
The tile adhesive contained a high concentration of VAE copolymers.
Dr. Peter Fritze, Construction Polymers Technical Service, WACKER POLYMERS

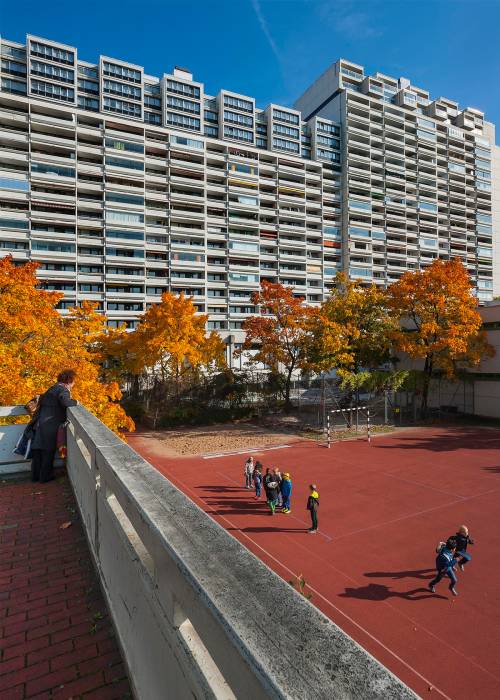
Together for a More Sustainable Future
In order to address rising demands for sustainability – from customers as well – WACKER got an early start launching products that help reduce humans’ environmental footprint. Use of the mass balance method to produce dispersible polymer powders based on renewable raw materials is one example here. The method makes it possible to reduce consumption of fossil resources without affecting the quality or properties of WACKER products. This involves using certified processes that allow WACKER to incorporate renewable raw materials in place of their fossil-based counterparts in the value chains of products such as VINNAPAS® eco. The VINNAPAS® eco grades produced in this way are chemically identical to the corresponding VINNAPAS® products.
ARDEX was one the first customers to use VINNAPAS® eco as a base material for parts of its production, making the company an early adopter of efforts to reduce its environmental footprint. The company also introduced the “ecobuild TECHNOLOGY” label so that its end customers could immediately see which products undergo comprehensive, systematic testing according to sustainability criteria. Examples of these criteria include the proportion of renewable raw materials, CO2 emissions during production and pollutants emitted after processing, with technical criteria such as product yield playing a role as well. The range of products bearing the label is constantly growing.
“ARDEX has always been passionate about sustainable construction. And that made it only natural for us to become one of the founding members of the GEV – the Association for the Control of Emissions in Products for Flooring Installation – and to help bring the Association to life,” notes Dr. Motzet. The non-profit organization works with consumers, skilled tradespeople and manufacturers to develop low-emission, high-quality products that bear the EMICODE® seal. This trademarked product-labeling system has become the central quality benchmark throughout the world and across product groups. “Over 96% of all ARDEX products now bear the EMICODE® label – due in part to raw materials from WACKER,” says Motzet in summary.