
Mind the Gap
The battery and its power storage ability can be seen as at the heart of electric vehicles. As battery capacities and voltage levels have steadily increased, thermal management has become a pressing matter. Gap fillers made from silicone-based thermal interface materials (TIMs) play a key role in keeping batteries cool even in extreme conditions.
The rechargeable battery – lithium-ion batteries are currently state of the art – serves as the energy storage device in an e-vehicle. As yet, there is no industry standard for e-vehicle batteries. Their designs vary but the basic components are the same: cells of different shapes, sizes and chemistry are stacked together to form modules. Several modules are then assembled into a pack and combined with an electronic battery management system to form a complete battery.
Staying Cool in Extreme Conditions
During storage, operation and charging of the battery, thermal management is needed. Silicones are perfect for this task: they can efficiently dissipate heat and they maintain their properties for a long period of time over a broad range of temperatures. They can also withstand mechanical stress, vibrations and temperature fluctuations.
Silicone Application Fields in a Traction Battery
Numerous silicone rubber products (shown in blue) are used in a typical traction battery. As (thermally conductive) gap fillers, gels, adhesives and pastes they serve many functions.
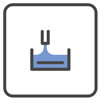
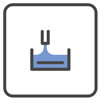
Bonding and damping of double cells to control vibrations
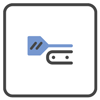
Insulation HV cable
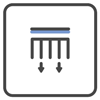
Cooling plate for battery-module heat management
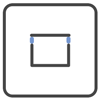
Battery housing seal
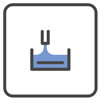
Encapsulated battery management system electronics
Silicones for Battery Modules
- Dissipate heat (thermal management)
- Couple cells with heat-sink elements (bonding)
- Couple cells for vibration control (bonding)
- Seal modules (CIPG – cured-in-place-gasket)
Silicones for Battery Pack System
- Dissipate heat (thermal management) / couple modules to achieve cooling
- Seal modules (CIPG – cured-in-place-gasket)
- Insulate high-voltage cables and seal connectors
Silicones for Battery Management System
- Protect electronic components (encapsulation / potting)
Silicones: Proven Solutions to a Hot Issue
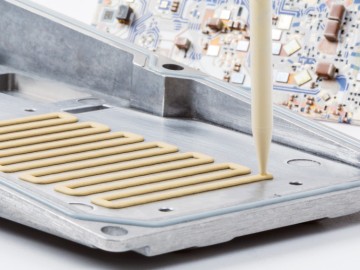
Temperature impacts the lifetime, performance, reliability, safety and cost of a battery. Heat dissipation to establish a uniform temperature has to occur at a rate that enables the battery to operate optimally within a desired temperature range. For example, lithium-ion batteries deliver their best performance at temperatures between 20 and 35 °C and must therefore be kept within that range.
Thermally conductive silicone plays an important role when it comes to cooling in the battery stack. It can be applied to the cells to dissipate internal heat, to bond them to each other or to the module housing, and to form a lager pack. The silicone also provides additional damping and vibration control and can be used as soft, flexible gap filler between uneven surfaces to handle broad temperature ranges.
Gap Fillers: The Answer to a Burning Question
Whether during charging or use, batteries generate and release levels of heat that need to be kept within an optimal range to ensure safety and help extend their lifetime. Soft, flexible, thermally conductive silicones dissipate this heat. With the SEMICOSIL® 96x TC series, WACKER has developed a range of thermally conductive gap fillers that are not only cost-effective and easy to process in automated processing lines but also offer safe functionality and high durability during the lifetime of the battery.