
The Power of E-Mobility
Besides traction battery and power electronics, the electric motor is one of the key components of electric vehicles. During operation, it can generate temperature as high as 200 °C, creating new challenges for the materials used. Silicones are a perfect fit: they resist mechanical and thermal stress, thus minimizing the risk of operational failure.
In conventional vehicles, the necessary torque is provided by a combustion engine. In electric vehicles, automotive manufacturers are using three-phase current motors instead. Such motors achieve high performances, despite their compact size and low weight. These are almost always so-called internal rotors: located on a shaft, the rotor rotates inside the stator, which is designed as a hollow body. The stator (i.e. stationary part) is fixed to the motor housing, whereas the rotor is mounted such as to rotate inside the housing. The housing is usually actively cooled.
A Look Inside an Electric Motor
The silicone products used here are shown in blue.


Coil impregnation with silicone resins
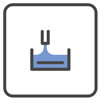
Potting coil connector ring / connection box
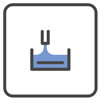
Potting coil connector ring / connection box

Coil impregnation with silicone resins / coil potting
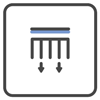
Active cooling with silicone oil

How an Electric Motor Works
The main components of the stator are the laminated core or armature – a stack of annular, punched iron plates with grooved inner rims – and a system of coils whose windings lie in the grooves. These coils, known as windings in motor technology, are supplied with three-phase current. They are designed for the three-phase current to generate a magnetic field whose direction constantly changes within the stator – the magnetic field spins around its axis. The rotor’s permanent magnets generate a permanent magnetic field, which follows the rotary field of the stator so that the rotor and motor shaft also rotate. The speed is determined by the frequency and the amount of torque by the amplitude of the three-phase current.
Hairpins Speed up Production

The windings can be designed in various ways. The traditional method is coil winding using a copper round wire – a complicated production method. The trend is currently moving towards hairpin technology, which involves forming coils from thin copper wire segments with a rectangular cross section. The segments are bent into hairpin shapes and inserted into the grooves made for this purpose in the laminated core, then bonded according to a certain pattern by soldering. Hairpin technology is suitable for the creation of fast, industrial-scale production.
Heat-Dissipation is the Key

During operation, heat is generated in the windings and the laminated core of the stator. The generated heat needs to be dissipated for various reasons: for one thing, the wire enamels used to coat the stator windings need to be protected against heat-induced aging. Second, permanent-magnet synchronous motors contain magnetic materials made from rare earth metals which can lose their magnetization at temperatures above 130 °C. Also, the heat dissipated from the electric motor can be readily deployed elsewhere, for instance to heat the passenger compartment and the windshield. This not only protects the battery, but also enables longer driving ranges, especially in winter.
Silicone Solutions to Optimize the Operation of the Electric Motor

Electric motor manufacturers are currently working on different heat-dissipation concepts. It is still unclear which one will prevail. However, it is clear that thermally conductive silicone products can play a key role. Tests are being conducted to establish whether the heat can be transported along the copper hairpins to the heat sinks via a thermally conductive silicone encapsulant such as the ELASTOSIL® RT 7xx TC series.
The use of heat-resistant silicone fluids to actively cool the electric drive components is currently under discussion. Compared with the conventional water/glycol mixtures used to cool modern combustion engines, chemically stable, non-flammable silicone fluids, such as POWERSIL® Fluid TR 50 which has long been used for cooling transformers, have the advantage of being electrically non-conducting. They also remain flowable down to -50 °C. Optimal cooling would therefore be ensured even during a cold start in the depths of Nordic winters.
Further WACKER products to optimize the e-motors functionality are the SILRES® H 60 C and H 62 C as 1 or 2 component solutions. Both products are ideal to impregnate electrical coils of motors and generators. They can be used to provide hydrophobic properties to porous materials and as binder for composites made of fibrous fillers, cloths, woven or non-woven reinforcing materials. This special products are low viscous at 60 °C so that it can be easily trickled into the gap between hairpins and laminations. As thermally conductive version SILRES® H 68 TC provides additionally heat conductivity of 1,1 W/mK.