
From Burghausen to NFL
Oct 01, 2019 Read time: approx. MinutesMinute
Play smart, play safe
Two US companies have developed a new type of helmet that will better protect players of American football against traumatic brain injuries and their long-term consequences. WACKER has provided assistance in the form of its ACEO® 3D printing technology.
Fans of the Pittsburgh Steelers called him “Iron Mike” because he was tough and hard – even on himself. Michael Lewis Webster, a professional footballer for 16 years, won the Super Bowl with the Steelers four times between 1975 and 1980. Though an inductee into the “Pro Football Hall of Fame”, it was not his extraordinary performances on the field that made him known outside of football circles and even beyond America’s shores. It was the tragic fate that befell him and that was so movingly portrayed in the movie “Concussion.”
After he retired from active sports, Iron Mike suffered from impaired speech, hearing and concentration, not to mention amnesia, along with hand tremors and depression. He spent periods of time living in his car, knocked out his own teeth when delirious and eventually died at the age of 50, officially because of a heart attack.
When Nigerian pathologist Dr. Bennett Omalu – portrayed in “Concussion” by Hollywood star Will Smith – autopsied Webster’s brain along with that of another footballer, he discovered a disease which is known in medical circles as chronic traumatic encephalopathy or CTE. Current medical opinion is that CTE is caused by repeated concussions or minor traumas to the skull and brain. It often takes the symptoms ten to twenty years to appear after the damage has been done. CTE occurs not only in footballers. It is increasingly afflicting boxers, as well.

Michael Lewis Webster, also known as “Iron Mike,” suffered from chronic traumatic encephalopathy after retiring from professional football. Multiple concussions or mild traumatic brain injuries, from which American football players frequently suffer, are considered to have caused his condition.
Enhanced protection
The National Football League (NFL) now actively promotes measures to prevent injuries that might have life-long consequences – such as concussions – or at least to treat them effectively. One such measure is the NFL’s “Play Smart. Play Safe.” initiative, launched in 2016 and involving a pledge of $100 million in support of independent medical research and engineering advancements. The NFL also announced an annual “HeadHealthTECH Challenge” which invites companies to submit proposals for improvements in football helmets and other protective equipment.
In late 2017, Baytech Products, based in Asheville, North Carolina, entered the second HeadHealthTECH Challenge because its founder and CEO, Robert T. Bayer, had conceived of a novel type of helmet. He had been supported in this by Brad Maloney, whose South Carolina-based company HelmetComp designs helmets for different types of sport, the military and the police.
“Our football helmet has a groundbreaking two-piece design, comprising an upper shell and a lower shell,” says Maloney. “The upper shell is attached to the lower section by flexible struts. The upper section can move in any direction after impact, and independently of the lower section and the football player’s head.” This design helps to absorb the energy of linear and rotational hits and prevent them from being transmitted to the head. “After impact, the upper shell returns to its original position,” he adds.
Bayer and Maloney entered the competition with a 3D-printed prototype, backed up by preliminary lab test results. The jury was so impressed that it declared Baytech a TECH Challenge II winner. What is more, the NFL awarded Baytech $178,000 for continued design advancements.
Bayer and Maloney have since partnered with a view to enhancing their helmet technology, called HitGard™, and achieving the goal of production release. After winning the challenge, they began injection molding the shells for the helmet, using high-impact absorbing foams for the inner shell and redesigning the face mask. All the while, they were determined to meet the requirements of the stringent lab tests commissioned by the NFL for checking a helmet’s safety and toughness. These include the use of a pneumatic ram tester to strike specific, predetermined points on the helmet with great force.
One such point is located in an area designed to protect the forehead, because American football players are particularly prone to frontal collisions. Directly below this point, the face mask is anchored in the helmet – here, too, collisions can generate enormous forces. The HitGard™ designers therefore specified that a special damping element made from thermoplastic polyurethane (TPU) be incorporated into this part of the helmet. “However, when the face mask was struck in the lab tests, this material fractured because it couldn’t absorb enough energy to cause it to deform,” says Maloney.

The highly physical nature of American football entails a high risk of injury.

ACEO® is based in Burghausen, from where it provides a global service for 3D-printed silicone elastomers. The silicone damper for the new helmet was designed there too.

The HitGard helmet is made up of two shells that can flex independently of one another upon impact. In this way, the shells are intended to protect the head more effectively from injury due to shocks.
Silicone damper
The product developer therefore started looking around for alternatives in spring 2018. His research led him to WACKER’s ACEO® 3D printing service with silicone rubber. He contacted the ACEO® team via LinkedIn. “After we had talked about the specifications the material would have to meet, Brad came straight out and asked if we could produce and ship such a damper to HelmetComp within ten days,” explains Egbert Klaassen, Global Marketing Director for WACKER’s ACEO® 3D printing solutions. The reason for the urgency: major tests had been scheduled with external testers.
Maloney’s request would have been an absolute impossibility for any company that produces silicone parts by conventional injection molding. That company would usually need eight to twelve weeks to create the corresponding mold – at huge expense – from the submitted CAD design files. The customer would then have to approve it before the silicone could be molded into the desired part. But thanks to the collaboration with the ACEO® 3D printing center in Burghausen, Maloney’s wish was quickly granted. The silicone damper, which has exactly the same properties as its injection-molded counterpart, was delivered ahead of the scheduled tests with a day to spare. Maloney installed it inside the helmet, which subsequently went on to pass the tests. Maloney’s take on the whole experience: “The WACKER ACEO® 3D printing service proved to be an extremely capable solution provider and will be supporting us further as we continue our development work.”
3D silicone printing saves time and money
The helmet designer is thoroughly convinced of the merits of using the ACEO® 3D printing service for developing and launching products onto the market. “Parts often need design tweaks after they have been made. 3D printing is a simple, rapid and cost-effective way of sourcing optimized parts – injection molding is a much more complicated process that would entail starting all over again.
There is one final, crucial step to be taken before the patent-pending HitGard™ helmets can be brought to market: Bayer and Maloney need to either partner with an established helmet maker or find a sponsor so that they can start up their own production. In view of the performance produced by the HitGard™ helmet, that should not take too long: its scores were among the highest ever achieved at any of the three major accredited US test labs.
Maloney believes that the future of the innovative, two-part shell design lies not only in American football. Cyclists, climbers, winter sports athletes and horse riders would all benefit from helmets that are better now than ever before at absorbing impact forces and torque. “The incredible properties of silicone rubber, its versatility and durability make it a prime candidate for this application,” stresses Maloney.

Helmet trends: from leather to high-tech (around 1950–2019)
How it works
HitGard’s patent-pending technology is a groundbreaking split-shell design consisting of an exterior upper and lower shell and an inner shell suspension system.
The exterior upper and lower shells are connected by highimpact absorbing struts. Upon impact, the upper shell can move independently of the head, thus absorbing/dispersing direct impact forces before the energy is transmitted to the head.
The upper shell absorbs both linear and oblique impacts before returning to its original position.
The inner shell suspension system is anchored to the exterior lower shell with high-impact absorbing materials. The player’s head is fitted inside the inner shell which is surrounded by an air void and thus is independent from direct impact energy to the upper shell.
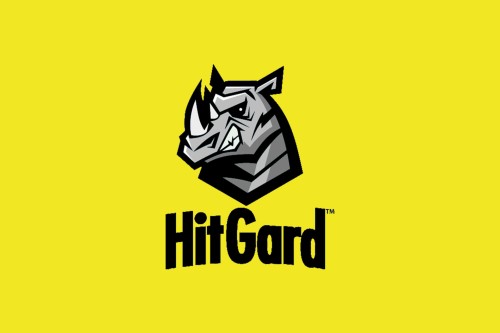
Mr. Egbert Klaassen
Global Segment Manager
Wound Care, Orthotics & Prosthetics
+49 1520 935 2545
egbert.klaassen@aceo3d.com