
Mikroinjektionspumpen
Kaum größer als ein Fingernagel
27.07.2021 Lesezeit: ca. MinutenMinute
Klein und genau
Automatisierte Dosiersysteme können mittlerweile das regelmäßige Spritzen wichtiger Medikamente wie Insulin übernehmen. Ihr Herzstück ist eine Mikroinjektionspumpe, deren Pumpgehäuse vom Polymerverarbeiter Trelleborg entwickelt wurde. Dafür brauchte es einen neuen Flüssigsiliconkautschuk, der scheinbar Unvereinbares verbindet: hohe Haftung und niedrige Gleitreibung.
Morgens, mittags oder abends: Menschen mit chronischen Krankheiten müssen ihren Körper rund um die Uhr überwachen. Stimmt der Insulinpegel im Falle von Diabetes? Brauche ich mehr Apomorphin im Falle von Parkinson? Fehlerhafte Über- oder Unterdosierungen können lebensgefährlich sein. Einige solcher Krankheiten sind durch Medikamente, die direkt unter die Haut gespritzt werden müssen, gut zu beherrschen – kleine Pikser mit lebenswichtiger Funktion. Tragbare Medizingeräte wie Insulin-Pens machen die schnelle und sichere Injektion von Flüssigmedikamenten im Alltag besonders praktisch. Sie passen in jede Handtasche und können unauffällig verwendet werden. Die Dosierung und die Zeitpunkte muss der Patient jedoch trotzdem genau im Kopf haben. Einen Schritt weiter gehen nun automatisierte Dosiersysteme.
Solche handtellergroßen Medizingeräte lassen sich etwa durch Klebepflaster direkt auf der Haut befestigen. An der Kontaktfläche zum Patienten befindet sich eine äußerst feine Nadel, die automatisch ausfährt und eine vorprogrammierte Arzneimittelmenge unter die Haut injiziert – ohne einen einzigen Handgriff des Patienten. Eine präzise Steuerung reguliert die gleichmäßige Abgabe weniger Mikroliter Wirkstoff über Minuten, Stunden oder sogar einige Tage. So verbessert sich die Lebensqualität Betroffener, da sie ihren Alltag flexibel und unbeschwert gestalten können. Herzstück eines solchen Medizingeräts ist eine winzige Mikroinjektionspumpe, die das lebensnotwendige Medikament zuverlässig fördert und exakt dosiert. Trelleborg wurde hier von einem weltweit führenden Anbieter von Pharma- und Medizinprodukten beauftragt, gemeinsam ein Pumpengehäuse aus Kunststoff und Silicon zu entwickeln.
Tief im Inneren des Bauteils sorgt dabei eine einzigartige Materialinnovation von WACKER für reibungslosen Betrieb. „Die extrem genaue Dosierung der Medikamente durch die Pumpe war ausschlaggebend für den Erfolg des gesamten Geräts“, betont Felix Schädler, Projektmanager für Innovation und Technologie bei Trelleborg, der maßgeblich an der Entwicklung beteiligt war.
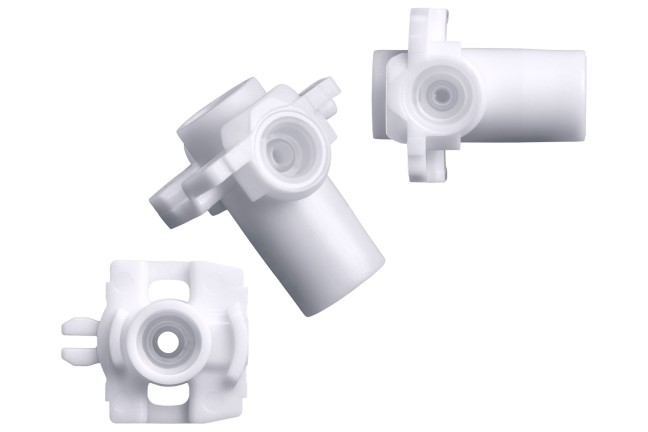
Solche winzigen Mikroinjektionspumpen, die aus Flüssigsiliconkautschuk im Spritzgießverfahren hergestellt werden, sind das Kernstück von automatischen Dosiersystemen, mit denen gleichmäßig flüssige Medikamente in den Körper des Patienten injiziert werden.
„Aufgrund der geringen Maße und Toleranzen konnte das Bauteil nur im Zwei-Komponenten-Spritzgießverfahren mit Dichtungen aus Flüssigsilicon hergestellt werden.“
Felix Schädler, Entwickler, Trelleborg
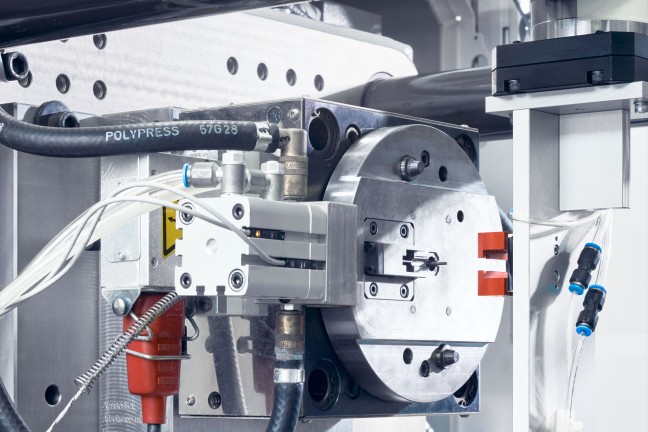
Mit solchen Werkzeugen wird der Flüssigsiliconkautschuk bei Trelleborg in Stein am Rhein verarbeitet – unter streng kontrollierten Bedingungen im Reinraum.
Kaum größer als ein Fingernagel
Die feingliedrige Mikroinjektionspumpe besteht aus einem zylindrischen Hohlkörper, in dem ein Kolben elektrisch auf und ab bewegt wird. Damit wird das Medikament aus einem Vorratsgefäß angesaugt und in die Injektionsnadel befördert. Das Pumpengehäuse gibt es in verschiedenen Varianten, die jeweils 2 μl beziehungsweise 10 μl Flüssigmedikament fördern können. Die kleinere Pumpe ist mit 15 mm Länge kaum größer als ein Fingernagel. Reibung, Abdichtung und die Verbindung von zwei verschiedenen Materialien auf engstem Raum waren von Anfang an eine Herausforderung für die Entwickler.
Neben dem Wunsch nach kompakter Bauweise legte der Kunde auch Wert auf möglichst niedrige Kosten, da es sich bei der Injektionspumpe in dem späteren Medizingerät um ein Einmalprodukt handelt. Sämtliche Elemente des Dosiersystems, die mit dem Medikament oder dem Patienten in Berührung kommen, müssen aus Sicherheitsgründen nach dem Gebrauch entsorgt werden. Dazu gehört auch die Injektionspumpe. Andere Bestandteile, wie etwa das Gehäuse, der Motor und die Batterie, können hingegen wiederverwendet werden.
„Aufgrund der geringen Maße und Toleranzen konnte das Bauteil nur im Zwei-Komponenten-Spritzgießen mit Dichtungen aus Flüssigsilicon hergestellt werden“, sagt Trelleborg-Entwickler Felix Schädler. Durchmesser vom Umfang einer Stecknadel machen das nachträgliche Einsetzen punktueller Dichtungen unmöglich. Das spezielle 2K-Materialverarbeitungsverfahren verbindet zwei verschiedene Werkstoffe effizient in einem Prozess. Die Idee war, dass eine fast komplette Innenauskleidung des Pumpenzylinders mit Elastomer den beweglichen Kolben abdichten und gleichzeitig schmieren sollte.
Die Verarbeitung von Flüssigsiliconkautschuken (Liquid Silicone Rubber, LSR) ist das Spezialgebiet von Trelleborg am schweizerischen Standort Stein am Rhein, wo im vollautomatisierten Betrieb Ein- und Mehrkomponenten-Spritzgussbauteile aus LSR gefertigt werden. Neben Produkten für den Automobilsektor und die Industrie gibt es in Stein am Rhein auch eine umfassende Reinraumfertigung für medizintechnische Anwendungen. In aktuell vier Reinräumen wird unter streng kontrollierten und überwachten Bedingungen produziert – mit steigender Tendenz.
Die Stellplätze durch die letzte Reinraumerweiterung vor fünf Jahren sind bereits komplett ausgelastet, sodass aktuell erneut vergrößert wird, wie Felix Schädler verrät. 2K-Spritzgießen war zwar bisher für Automobilbauteile gängig, in Medizinanwendungen aber weniger gefragt. Das ändere sich gerade, da die Branche zunehmend höherem Druck hinsichtlich Risiko- und Kostenverringerung ausgesetzt ist, so der Experte. „Außerdem sind mittlerweile selbsthaftende LSR-Typen auch für Lebensmittelkontakt- und Medizinanwendungen verfügbar“, begründet Schädler. „Das hat den 2K-Spritzguss für diese Anwendungen überhaupt erst möglich gemacht.“
Dem können Dr. Ulrich Frenzel und Dr. Florian Liesener, beide Laborleiter in der Anwendungstechnik von WACKER in Burghausen, nur zustimmen. Sie arbeiten eng mit Trelleborg zusammen und können im Falle der Mikroinjektionspumpe auf eine ganz besondere Materialentwicklung zurückblicken.
Nachdem sich TPE für diese spezifische Anwendung als ungeeignet erwiesen hatte, setzten Schädler und sein Team zunächst auf den selbsthaftenden Flüssigsiliconkautschuk SILPURAN® 6700. Unter der Marke SILPURAN® bietet WACKER seit etwas über zehn Jahren speziell für die Medizintechnik entwickelte Silicone an. „Verglichen mit Siliconen für technische Produkte verwenden wir für sensible Anwendungen spezielle Rezepturen, da besondere Reinheitsanforderungen erfüllt werden müssen“, präzisiert Chemiker Frenzel.
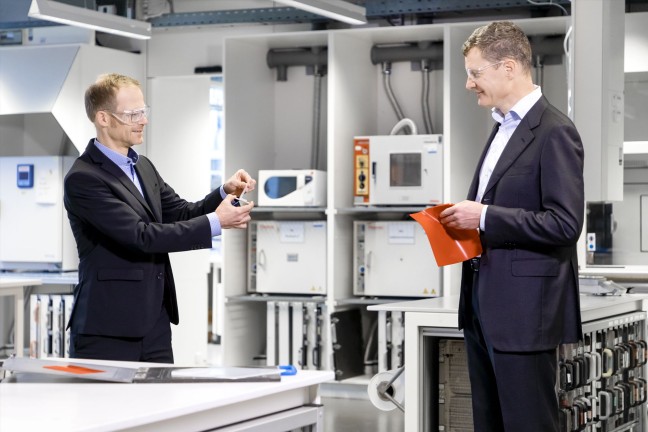
Dr. Florian Liesener (l.) und Dr. Ulrich Frenzel aus der Anwendungstechnik von WACKER.
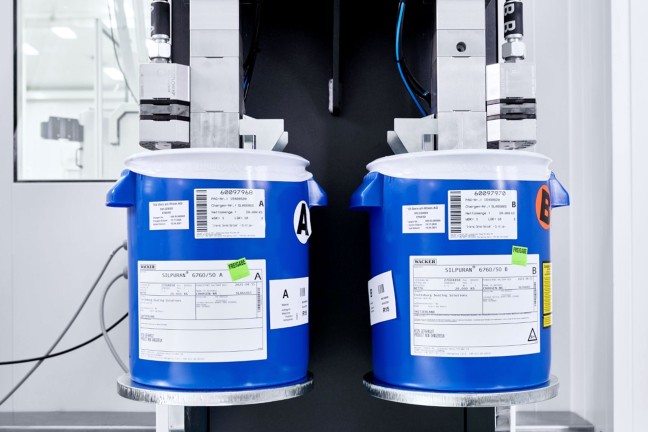
In solchen Gebinden, die direkt an der Maschine bereitgestellt werden, wird der zweikomponentige Flüssigsiliconkautschuk an den Verarbeiter geliefert.
Schnell und prozesssicher
Mit SILPURAN® 6700 kam 2008 die erste selbsthaftende Flüssigsiliconreihe von WACKER speziell für die Medizintechnik auf den Markt. Die sehr gute Anbindung dieser Produkte an zahlreiche Thermoplaste prädestiniert diese Typen für das 2K-Spritzgießen. Direkt angespritzt und fest verbunden, lassen sich damit auch für die Medizintechnik Funktionsbauteile in Großserie kostengünstig, schnell und prozesssicher herstellen.
In Zusammenarbeit mit dem Medizinproduktehersteller und dem Elastomerlabor von Trelleborg in Stuttgart bestand SILPURAN® 6700 unter anderem langfristige Einlagerungstests mit dem Medikament. Da die Medikamente mit den Dichtungen in direkten Kontakt kommen, durfte es keinerlei Wechselwirkungen geben.
Beim Funktionstest der Pumpe stellte sich jedoch heraus, dass die Reibung zwischen dem Kolben und den Zylinderoberflächen aus SILPURAN® 6700 zu hoch war. Schon kleinste Über- und Unterdosierungen der Medikamente können beim Patienten zu lebensgefährlichen Situationen führen, daher ist ein ruckelfreier Betrieb der Pumpe essenziell. Bei hoher Reibung zwischen Kolben und Zylinder wäre mehr Kraft für die Pumpbewegung notwendig gewesen, was einen anderen Antrieb und damit ein insgesamt größeres Gerät erfordert hätte. Alternativ hätte der Kunde Schmiermittel verwenden können. Diese würden jedoch zwangsläufig mit dem geförderten Medikament in Kontakt kommen und es möglicherweise beeinträchtigen oder im schlimmsten Falle verunreinigen. Aus dem gleichen Grund schied auch eine Verwendung ölausschwitzender Silicone aus, wie sie WACKER etwa für Anwendungen im Automobilbau anbietet. Diese Typen weisen zwar sehr geringe Reibungswerte auf, sind aber für medizinische Anwendungen unbrauchbar. Schließlich gilt es unbedingt zu verhindern, dass sich Öl mit dem Medikament vermischt und einem Patienten ungewollt subkutan injiziert wird.
Langjährige Partnerschaft
Die Materialspezialisten von WACKER fanden aber eine Lösung, die ohne Öl auskommt. „Aufgrund unserer langjährigen, sehr guten Partnerschaft haben wir uns bei dieser Herausforderung an die Werkstoffentwickler von WACKER gewandt“, berichtet Felix Schädler von Trelleborg. Die WACKER-Chemiker hatten sehr schnell erste Ideen für eine passende Neuentwicklung und innerhalb nur eines Jahres konnte eine neue Werkstofftechnologie zur Marktreife gebracht werden.
„Wir hatten bereits Flüssigsilicone mit selbsthaftenden Eigenschaften im Portfolio sowie Produkte mit niedrigen Reibungskoeffizienten, aber keine für sensible Anwendungen, die beides zusammen bieten“, erinnert sich Dr. Liesener aus der Anwendungstechnik von WACKER. „Die Mikropumpe war für uns daher die richtige Gelegenheit, beide Eigenschaften in einem Silicon zu kombinieren.“
Dem LSR sollten dabei physikalisch scheinbar unvereinbare Eigenschaften verliehen werden: hohe Haftung und geringe Gleitreibung, gewissermaßen Festhalten und Loslassen gleichzeitig. Unmöglich, könnte man meinen, „und doch wurde es von WACKER nachweislich ohne Probleme chemisch gelöst“, berichtet Felix Schädler anerkennend.
Von der Werkstofftechnologie wollen die Materialexperten nur so viel verraten: Ein zusätzlicher Rezepturbestandteil modifiziert das selbsthaftende Silicon derart, dass die Reibung gegenüber dem Materialpartner deutlich reduziert wird. Auch ohne Zusatz ausschwitzenden Öls bildet sich dadurch eine dauerhaft reibungsmodifizierte Oberfläche.
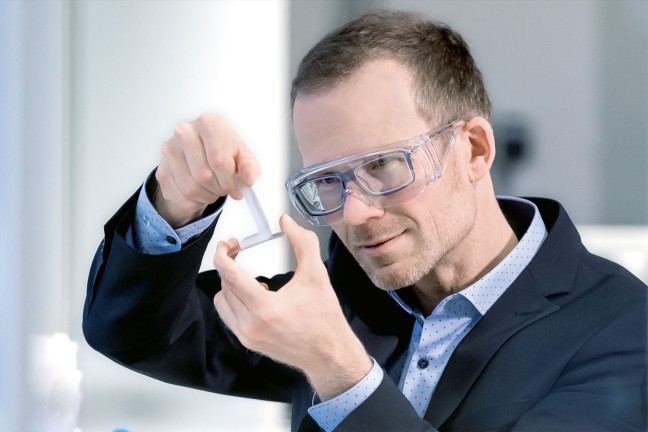
Dr. Florian Liesener ist bei WACKER für die Entwicklung hochspezialisierter Flüssigsiliconkautschuke verantwortlich, die nach den Bedürfnissen der Kundenindustrien maßgeschneidert werden.
„Wir hatten Fertigungstoleranzen von zwei Hundertstelmillimeter einzuhalten – das war eine echte Herausforderung.“
Felix Schädler, Projektmanager, Trelleborg
Einzigartig auf dem Markt
„Das ist die entscheidende Voraussetzung für diese Anwendung“, sagt Florian Liesener. Im Jahr 2016 wurde die Materialentwicklung unter dem Namen SILPURAN® 6760/50 zum ersten Mal öffentlich vorgestellt. Bis heute ist es das einzige selbsthaftende, reibungsmodifizierte Flüssigsilicon mit Marktreife und Biokompatibilitätszertifikaten.
Neben der erfolgreichen Zusammenarbeit bei der Materialentwicklung bescheinigt Siliconexperte Liesener den Fachleuten bei Trelleborg enorm viel Know-how und Erfahrung beim Produktionsprozess. Der feste Pumpenzylinder besteht aus einem glasfaserverstärkten technischen Kunststoff. Er wird zuerst in Spritzgießwerkzeug gefertigt. In einem zweiten Schritt wird die Zylinderinnenwand dann hauchdünn mit SILPURAN® 6760/50 ausgekleidet. „Wir hatten dabei Fertigungstoleranzen von zwei Hundertstelmillimeter einzuhalten“, erinnert sich Schädler, „und die Materialien selbst schwinden teilweise schon um bis zu 35 Prozent.“
Um dieses Problem und weitere kritische Produktionsaspekte zu lösen, hat Trelleborg das Bauteildesign zusammen mit seinem Kunden so verbessert, dass es technisch überhaupt machbar wurde. „Dafür mussten wir auch unsere Herstellungstechnologie weiterentwickeln“, so Schädler. Die Injektionspumpe wird im Reinraum gefertigt und gehört aktuell zu den kleinsten 2K-Bauteilen, die Trelleborg am Standort Stein am Rhein herstellt.
Kleiner wäre sie nach dem heutigen Stand der Fertigungstechnik nicht zu produzieren, da sind sich die Experten einig. SILPURAN® 6760/50 hat in dem kompakten Gerät zur Arzneimittelabgabe eine wichtige und sichere Doppelfunktion. Sie mag für die Anwender unsichtbar sein, ermöglicht ihnen aber ganz neue Freiheiten.
Kontakt
Mehr Informationen zum Thema erhalten Sie von
Herr Dr. Florian Liesener
Leiter Technisches Marketing Engineering Silicones
WACKER SILICONES
+49 8677 83-3566
Nachricht senden