WACKER Presents Silicone-Based Solutions for Electromobility and Medical Applications
Silicone Expo Europe
Munich, Feb 28, 2024
At Silicone Expo Europe, which begins today, the WACKER Group is showcasing silicone-based product solutions for specific industrial sectors. The focus is on silicone gels for wound care, non-postcuring liquid silicone rubber for the food industry and medical technology, and self-adhesive liquid silicone rubber grades that adhere to polycarbonate and other high-performance plastics. Products for electromobility applications and resource-efficient silicones are also in the limelight. Silicone Expo Europe is taking place from February 28 to 29 in Amsterdam, the Netherlands.
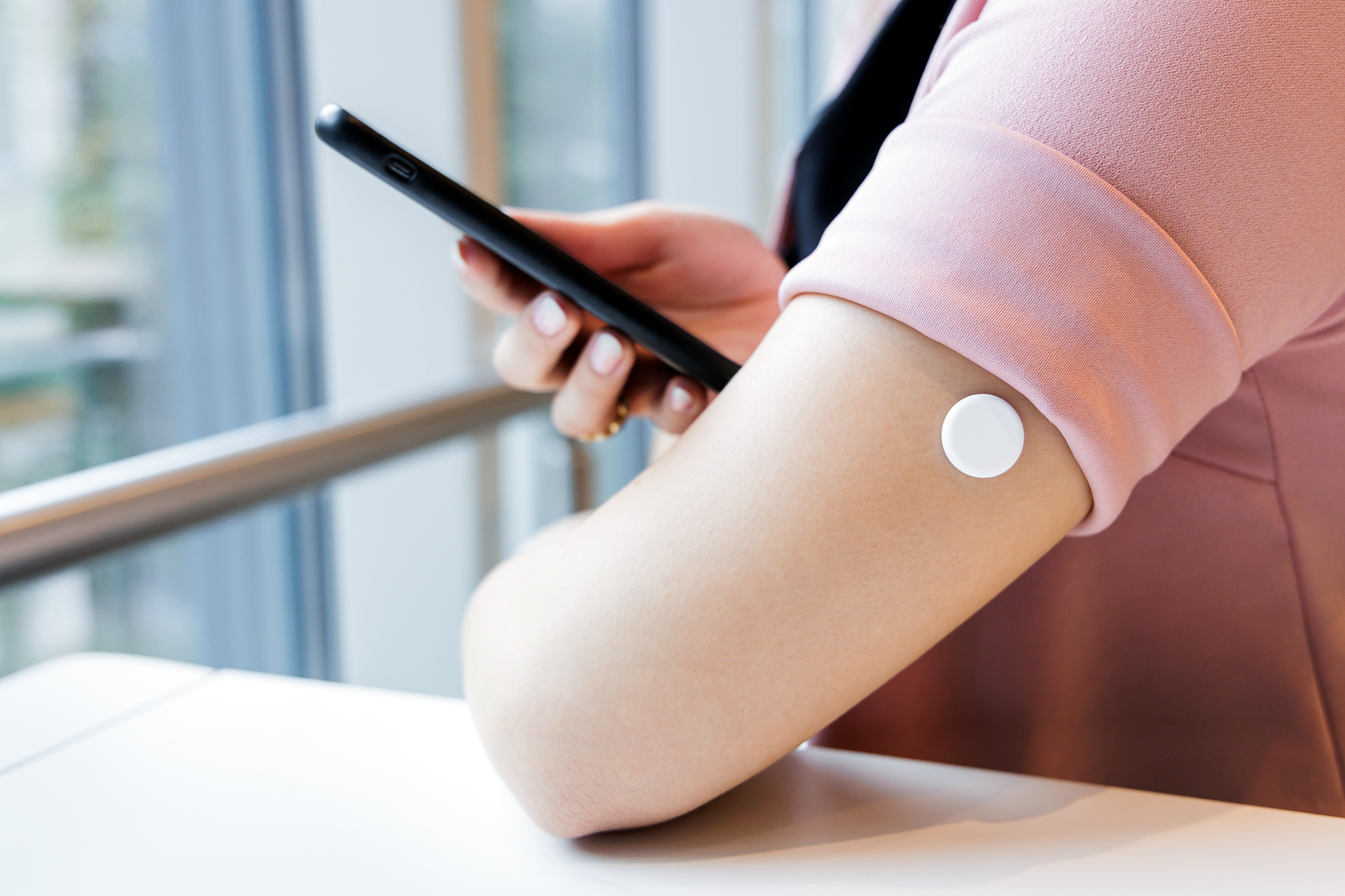
SILPURAN® silicone adhesives have a proven track record over many years in the field of atraumatic wound dressings. As an adhesive layer, they enable secure and gentle fixation of wound dressings to the skin. SILPURAN® adhesive gels adhere so gently that pain-free removals of dressings are possible.
WACKER will be using Silicone Expo to showcase not only its tried-and-tested product range, but also a silicone adhesive that adheres much more strongly than previous grades. SILPURAN® 2124 achieves an adhesive force of 6.0 newtons per 2.5 centimeters, determined in the 90° peel test on steel in accordance with EN 1639. This means that adhesion is so strong that the gel is suitable both for wound care and for fixing wearables, i.e. sensors, catheters, cannulas or other medical devices. SILPURAN® 2124 is biocompatible according to selected tests in accordance with ISO 10993 and USP, Chapter <88>, Class VI. It can be sterilized with ethylene oxide.
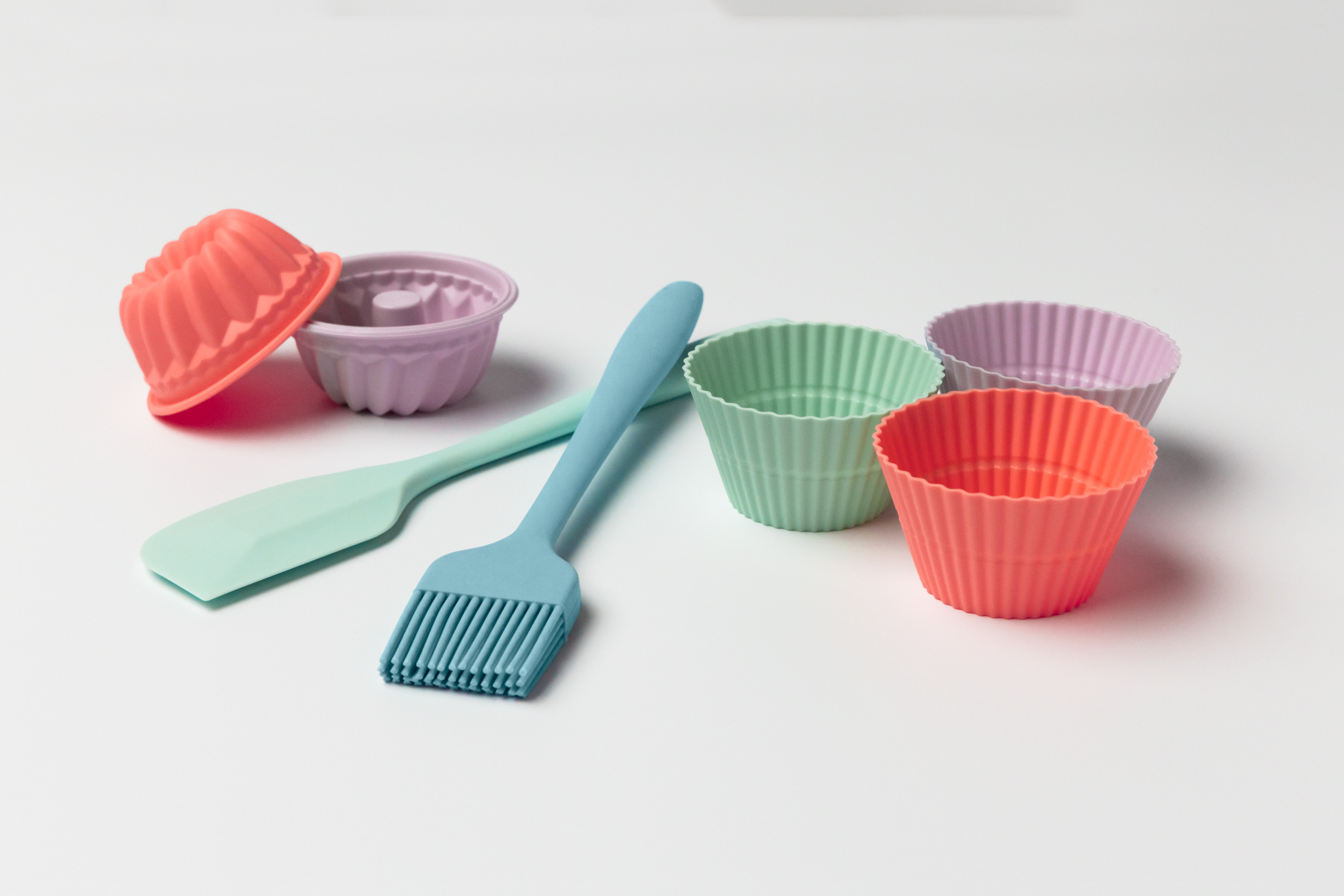
ELASTOSIL® LR 3078 – Self-Adhesive on Polycarbonate and Other High-Performance Plastics
Another highlight is the ELASTOSIL® LR 3078 product line. This self-adhesive liquid silicone rubber cures rapidly and establishes a firm bond with the polycarbonate thermoplastic. This makes it easy to produce hard-soft combinations using two-component injection-mold-ing processes. The adhesion system developed by WACKER is free of bisphenol A structures. Cured rubber products of ELASTOSIL® LR 3078 have been successfully tested for biocompatibility.
The product also offers good adhesion properties as regards other high-performance plastics that are difficult to process using 2K methods, such as polyphenylene ether (PPE), polysulfone (PSU), polyether sulfone (PESU), polyphenyl sulfone (PPSU) and polyether imide (PEI). Thanks to its good adhesion, ELASTOSIL® LR 3078 paves the way to cost-effective large-scale production of respiratory and anesthesia masks, drug delivery systems or devices for minimally invasive examinations and operations.
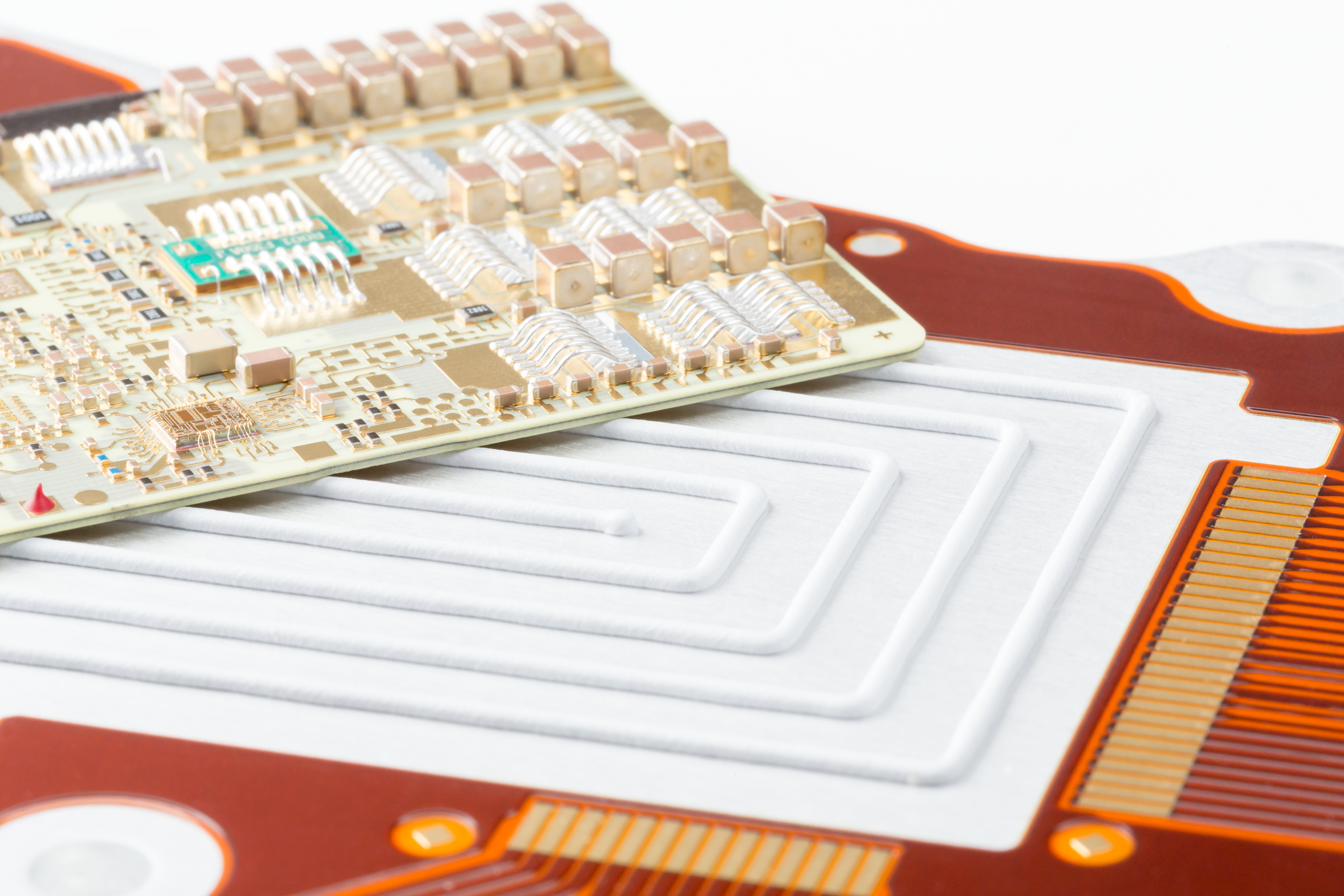
Non-Postcuring Liquid Silicone Rubber
Silicone rubber frequently undergoes postcuring after processing. During this procedure, the cured silicone elastomer is heated in a well-ventilated oven for several hours to temperatures of up to 200 °C. This eliminates volatile components while enhancing the strength of the silicone rubber. However, this is an expensive step in production that not only consumes a lot of time and energy, but also interrupts the flow of a highly automated production process.
WACKER has now developed a line of non-postcuring liquid silicone rubber grades under the name ELASTOSIL® LR 5003, which is parti-cularly suitable for the large-scale manufacture of products in the food industry and other sensitive areas. As far as their volatiles content is concerned, molded parts made from such silicones comply with the limits stipulated by the German Federal Institute for Risk Assessment (BfR) even without postcuring. They also meet the requirements of the U.S. Food and Drug Administration (FDA) for food contact products. This means that products such as reusable drinking straws, baking pans, dough scrapers and other items can be produced very efficiently. ELASTOSIL® LR 5003 may be additionally postcured in order to achieve even greater strengths and an even lower volatiles content.
ELASTOSIL® LR 5003 complements ELASTOSIL® LR 5040, which is also a non-postcuring liquid silicone rubber. Even without postcuring, the latter exhibits a high degree of tear resistance, a property required, for example, for drinking and soothing teats, teething rings and other babycare articles that have to withstand high mechanical stresses.
Silicones in Electromobility
Frost, heat, moisture, vibrations, high electrical voltages and charging currents – materials used in electric vehicles have to withstand a lot. Silicones from WACKER are capable of doing so. They prove their worth in many areas of application, whether in electrical systems, electronics or the thermal management of batteries. Silicone Expo Europe gives WACKER an opportunity to demonstrate how silicones are ensuring a sustainable transition to electromobility. Take the following two examples:
- Charging currents and the resulting waste heat of battery-operated vehicles are constantly on the rise, with voltages of up to 800 V and charging currents of up to 350 A no longer uncom¬mon. For this reason, the automotive industry needs extrudable materials that will reliably retain their electrical insulation proper¬ties over a very broad range of temperatures and over long periods of time. Silicones such as ELASTOSIL® R plus 4305, a solid silicone rubber, are an ideal fit for applications such as these. When formulated with a corresponding heat stabilizer, the product can withstand temperatures of up to 200 °C, without substantial changes in either its mechanical properties or its electrical characteristics.
- Electric vehicles normally use lithium-ion batteries as their power source. These are usually installed below the passenger com-partment, where they occupy most of the floor space. A thermally conductive gap filler is needed to provide thermal coupling between the battery modules and the heat-dissipation system. It must be aging-resistant to prevent premature battery failure and must lend itself to rapid application to large surfaces. For this, WACKER has developed flowable, silicone-based gap fillers that can be injected quickly and yield perfect results even on large areas, thereby facilitating high-speed large-scale production.
Resource-Efficient: ELASTOSIL® eco
ELASTOSIL® eco is another product that WACKER will be presenting at Silicone Expo. These silicones are produced in a resource-efficient manner and stem from plant-based methanol derived from non-fossil sources. ELASTOSIL® eco products are certified to the REDcert2 standard, thereby ensuring the traceability of renewable raw materials along the entire production process.
Presentation on Silicone Adhesives
WACKER will also be giving a technical presentation at Silicone Expo Europe. On February 29, Andrea Bogner, Senior Marketing Manager Industrial Solutions at WACKER SILICONES, and Peter Serrano, Global Segment Market Director for Performance Solutions at Loparex, a leading producer of paper and film release liners, will be talking about the combination possibilities of high-performance silicone adhesives and release films. The lecture starts at 1:10 p.m.
Contact

Wacker Chemie AG
Media Relations
Florian Degenhart
Tel. +49 89 6279-1601
Email florian.degenhart@wacker.com
Send Message
Download
Press Information
(PDF | 329 KB)