Integrated production means taking the byproducts of chemical processes, such as waste gas, wastewater, solid waste and waste heat, and using these as starting materials for other products.
Integrated Production at WACKER
Putting sustainability into practice through closed material loops is one of WACKER’s major strengths. Through the highly integrated production systems at its major sites in Burghausen, Nünchritz, Charleston and Zhangjiagang, WACKER has created a unique production strategy for conserving energy and resources.
Incorporating environmental protection into the production process involves the following:
- Integrated energy solutions
- Integrated material systems
Integrated Energy Solutions
Integrated energy solutions are based on the principle of taking the waste heat generated in production and using it in downstream chemical processes. Two examples here include generating steam from waste heat and preheating feed water for the production of deionized (DI) water.
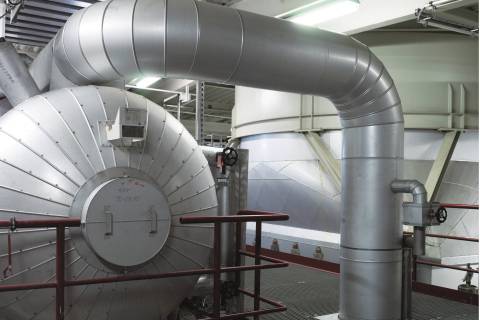
Generating Steam from Waste Heat
Heat released during chemical reactions is used for producing steam, which, in turn, serves as heating or process steam in other plants – resources that then do not need to be generated from primary fuels at the power plant.
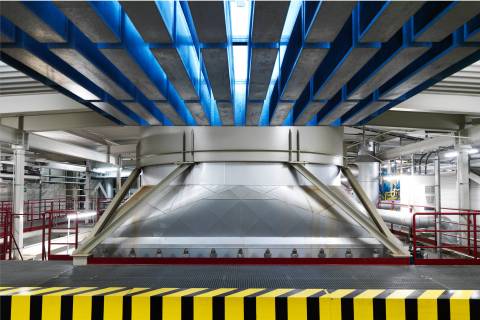
Preheating Feed Water for Deionized (DI) Water Production
Because feed water is too cold for producing DI water effectively, it is warmed using waste heat from turbines and refrigeration units. This saves energy and cooling water, while also helping cool the turbines and refrigeration units.
Integrated Material Systems
The principle underlying WACKER’s integrated production system is to conserve raw materials by introducing byproducts into material loops. Byproducts generated in a given process are either treated and fed back into that process or used as raw materials for other processes. Many different production chains fit together like cogs in a clockwork mechanism to drive the overall material loop of the integrated production system. Examples here include our integrated hydrogen chloride, silicon and acetic acid production systems.
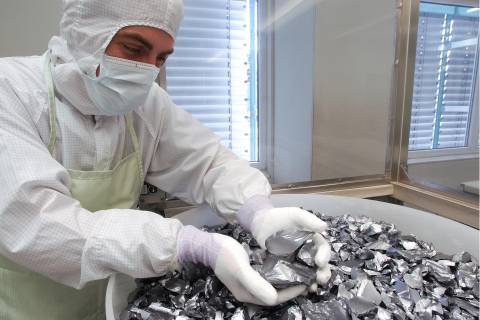
The Relationship between the Hydrogen Chloride and Silicon Production Systems
Hydrogen chloride production requires a great deal of energy, and the lion’s share of this is obtained by recovering hydrogen chloride from downstream production processes. Within the integrated silicon production network, for instance, silicon is converted to chlorine-containing intermediates from which chlorine-free end products such as silicones, hyperpure silicon and pyrogenic silica are produced – this, in turn, yields hydrogen chloride, which is then recovered. Hydrogen chloride and steam are also generated from chlorine-containing waste gases.
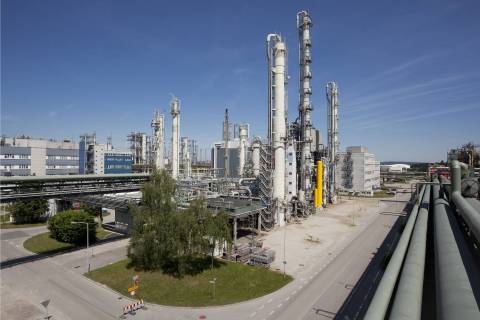
Integrated Acetic Acid Production
Acetic acid is a recurring building block in our integrated production system, and is recovered from various recycling loops along with methanol, methyl acetate and ethylene. This system eliminates the need for procuring up to 1,150 tank cars of raw materials each year – the equivalent of a train 19 km long. Acetic acid and ethylene are used as starting materials for vinyl acetate monomer (VAM) – the raw material for nearly all of the products sold by WACKER POLYMERS.
We are constantly working to optimize our integrated production system. We also analyze and test ways of extending the circular economy so that we can feed materials from our customers, partners and suppliers into this loop along with our own WACKER materials.

Contact
We would be happy to assist you with any questions you may have concerning sustainability at WACKER.
Send a message