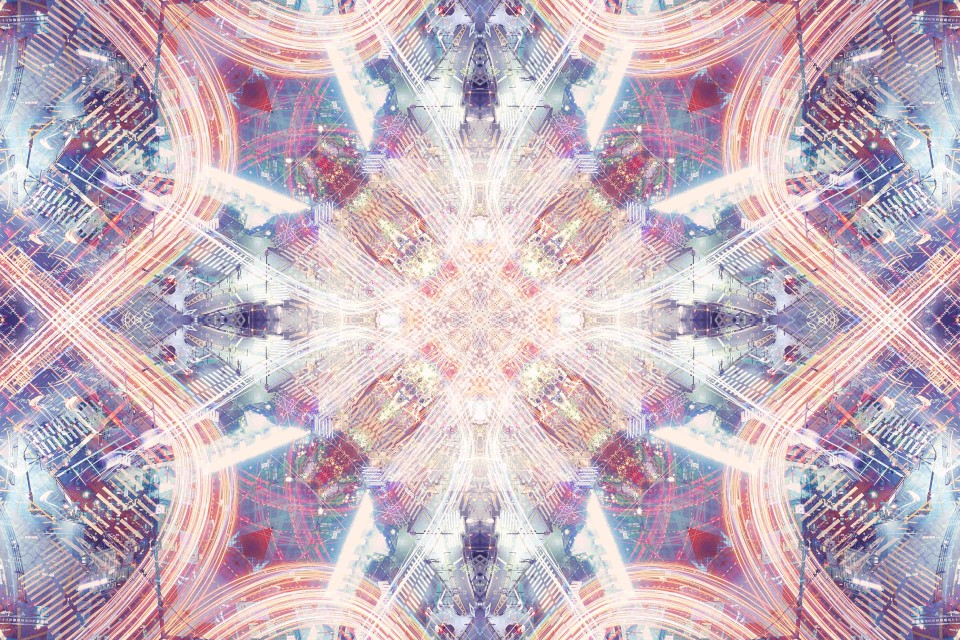
Silicone-Based TIMs Have a Long and Successful Track Record in Power Electronics.
May 26, 2020 Read time: approx. MinutesMinute
Keeping Cool with TIM
Electric vehicles need efficient thermal management to keep traction batteries, electric motors and power electronics from overheating. Thermal interface materials (TIMs) made from silicone do precisely that.
Any owner of a cellphone will tell you after a call that the battery gets warm. So imagine how hard it must be to effectively dissipate all the heat generated by the various components of an electric vehicle while it is being driven on the road or charged. “Thermal management is crucial for the battery in its role as the power source,” says Peter Walter, marketing manager in the Industrial Solutions team at WACKER SILICONES.
Lithium ion batteries only deliver their best performance at temperatures of between 20 and 35 degrees Celsius. “Consequently, to ensure an acceptable performance and life span, they need to be prevented from overheating,” notes Walter. The power electronics are another source of heat. This thermal energy needs to be dissipated quickly and effectively as well if the component is not to suffer heat damage or fail completely. Thermal interface materials (TIMs) are used to bridge the gap that exists between the component to be cooled and the heat exchanger or heat sink.
“Air is a very poor heat conductor and so is unsuitable for dissipating heat,” says Dr. Philipp Müller, in charge of customer service in the Industrial Solutions team at WACKER SILICONES. So, inserting a thermal interface material into the gap creates a thermally conductive connection between heat source and heat sink. “The thermal contact between the components lowers the heat transfer resistance,” adds Müller.

Battery indicator in an electric car: the faster the battery charges, the greater the heat flux is inside the battery pack that has to be dissipated effectively.

Silicones for battery protection: In vehicles fitted with alternative drives, many components need to be afforded reliable protection against environmental factors by way of silicone rubber compounds. The requirements are high due to the extreme conditions, such as sudden temperature changes, vibrations or contact with oils and chemicals.
Successful Track Record
Thermal interface materials are commonly made from polymers which have a high filler content of thermally conductive inorganic substances. The base polymer may be an organic polymer or a silicone. The necessary level of thermal conductivity is achieved by raising the filler content to over 90 percent in most cases. The fillers employed are typically ceramic metal oxides, such as aluminum oxide. They ensure that the TIM remains electrically isolated, a requirement essential for use in close proximity to live components.
Silicones are widely known for their aging resistance – even upon exposure to high or low temperatures. Unlike organic polymers, they undergo very little change in physical or technical properties over the temperature range -45 to +150 degrees Celsius and above. They are also more flame-resistant than organic polymers.
A further characteristic of silicones is their low surface energy. Liquid silicones, for instance, will wet nearly all solid surfaces. “This makes silicone-based TIMs easier to work with, as they will fill in even the tiniest irregularities in the substrate surfaces,” explains Müller. Aging resistance and flame resistance are also the main arguments in favor of using thermally conductive silicone products in vehicles fitted with all-electric drives – even for assemblies operating at temperatures which do not necessarily require silicone.
Silicone-based TIMs have a long and successful track record in power electronics. The task of power electronics is to control and convert electric power. Inverters, for example, convert direct current into alternating current and vice versa while voltage converters change voltage levels. Power module components such as IGBTs (integrated gate bipolar transistors) can reach temperatures greater than 100 degrees Celsius in operation. The power losses can exceed 100 W/cm² – more than the power density emitted from the surface of a cooker hob on full power.
Overheating can damage the sensitive semiconductor structures and so lead to aging and eventually to component failure. Such failures can be prevented by actively cooling the printed board and IGBT assembly. “At operating temperatures above 100 degrees Celsius, silicone-based TIMs are the materials of choice for thermal coupling, because organic polymers couldn’t withstand the heat for a protracted period,” explains Müller. Effective cooling can be achieved by matching the component design to a thermally conductive gap filler from the SEMICOSIL® 96x TC series, to a heat-sink paste (e.g. SEMICOSIL® Paste 40 TC) or to a heat-sink adhesive (SEMICOSIL® 9754 TC).
Easy Application
Many silicone-based thermal interface materials are available in paste form. As they are shear-thinning compounds, they do not sag when at rest, but will flow when placed under shear. They are dispensed onto the heat sink in the form of a bead. The assembly to be cooled is then mounted on top and pressed into place. Pourable types are also available in the form of resins and potting compounds.
Gap fillers cure in the gap to yield a relatively soft, elastically deformable pad that follows the contours of the surfaces exactly. Such gap fillers can even out surfaces with roughness values in the millimeter range which occur especially with large substrates. This distinguishes them from prefabricated pads, which have a specific thickness and are therefore unable to accommodate large tolerances.

Use of a silicone-based gap filler: Air is a poor heat conductor and so is unsuitable for dissipating heat.
Thermally conductive potting compounds are used for complex surfaces. They transport the heat to the heat sink while simultaneously protecting the surfaces from environmental factors. Such products are applied by potting, with dipping or pouring also being used in the case of resins.
“So, what we have done is to take our silicone products with their successful track record in the thermal management of power electronic modules and to develop them for use in the electromobility sector,” says Walter. “The company is continually optimizing these products, and especially their ease of processing, to make them suitable for mass production.”
The primary requirement here has been to adjust the rheological properties of the paste-like compounds so that they can cope with high-speed, highly automated car production. The relevant parameters are the molecular chain lengths and the type of liquid silicone polymers as well as the size and shape of the filler particles.

By creating a thermally conductive connection between the heat source and the heat sink, thermal interface materials (TIMs) enhance conductivity.
Mr. Peter Walter
Senior Marketing Manager
Industrial SolutionsWACKER SILICONES
+49 89 6279-1547
peter.walter@wacker.com