
“With thermal insulation, we can influence climate protection in a big way”
Interview with Peter Summo
Peter Summo, head of WACKER POLYMERS, talks about sustainable solutions for the construction industry – and why an unobtrusive white powder plays a key role in functioning insulation systems.
Mr. Summo, why does WACKER POLYMERS expect the demand for increased climate protection in construction and more energy-efficient buildings to generate growth for its dispersible polymer powders business?
Peter Summo: Buildings consume a lot of energy. Overall, the construction and operation of buildings account for about 40 percent of global primary-energy consumption, and at the same time they represent 38 percent of global CO2 emissions, according to a UN report. The main factors here are heating and air conditioning. Currently, much of the energy input is lost before it is used. The uninsulated exterior walls of a single building account for up to 40 percent. But if old buildings are made more energy efficient and higher energy efficiency standards are applied to new buildings as well, then we can really influence climate protection in a big way.

External thermal insulation composite systems are usually attached to the wall with an adhesive mortar that is cured with VAE binders from WACKER POLYMERS.
Isn’t well-functioning building insulation especially important in colder regions of the world?
Insulation applied to the outside does ensure that the walls do not cool down too much in the winter months – that’s right. But it also prevents houses from heating up unnecessarily on hot days, thus reducing the amount of energy that would otherwise be needed for air-conditioning. We were able to demonstrate this in a model house project in Dubai, which we conducted there with state-owned Dubai Central Laboratories. “Building insulation can reduce the electricity consumption of air-conditioning systems by as much as two-thirds.” Thermal insulation therefore makes perfect sense even in hot regions of the world.
WACKER POLYMERS produces polymer binders based on vinyl acetate-ethylene dispersions and dispersible polymer powders (VAE). How can these products contribute to more energy efficiency in construction?
The composite system must be carefully bonded to the walls and the individual layers must adhere firmly to each other to produce the optimum insulating effect. Most external thermal insulation composite systems are made of foamed polystyrene. To ensure adhesion to the wall, a so-called adhesive mortar is needed, which is modified with our polymeric binders. At the same time, our polymers are used not only at the base but also on the surface of the thermal insulation. They make the thin and rather brittle exterior plaster flexible, and thus protect the insulation system from cracks through which rainwater can penetrate, for example, and from mechanical damage such as that caused by hail. WACKER binders are therefore the key to an insulation system that offers long-term durability.
There are also other thermal insulation systems for new buildings. For example, bricks that are already insulated ex works – namely from the inside – with glass fibers, mineral wool or the very porous volcanic rock perlite. What then is the point of external thermal insulation composite systems?
Not all new buildings have insulated brick walls. For instance, many also have concrete exterior walls for structural reasons. In Europe, though, the greatest potential is to be found not in new construction, but rather in improving the energy efficiency of existing buildings. The figures paint a clear picture. According to a study by the European Commission, about three quarters of existing buildings are currently not energy efficient. Yet, under the European Green Deal, greenhouse gas emissions in Europe are to be reduced by more than 55 percent by 2030, compared to 1990 levels. The EU is also aiming to be net zero by 2050. To achieve these goals, some major obstacles will have to be overcome.
What does that mean for the construction industry in concrete terms?
We anticipate a veritable wave of renovations. The European Commission has also published figures in this regard showing that 35 million buildings will require energy-efficient refurbishment by 2030. The Commission estimates that this will entail annual investments of 275 billion euros.
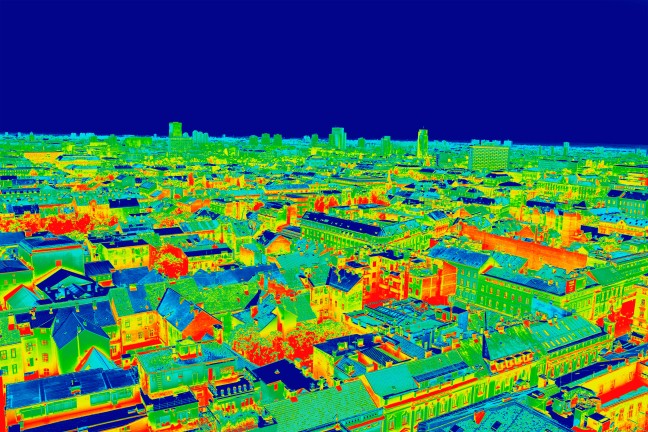
Thermal imaging footage of a major European city shows significant heat loss through windows and masonry. However, many roofs on old buildings are now insulated.

Structure of an external thermal insulation composite system – VINNAPAS® dispersible polymer powder imparts high flexibility and impact resistance to mortar. This is particularly important in the exterior render of an external thermal insulation composite system to compensate for stresses caused by weathering. At the same time, the VAE polymer acts as a stable yet flexible connection between the individual layers of the protective facade insulation.
Is building insulation, especially for existing buildings, a specifically European issue?
It is trending strongly in other regions, too. China, for example, plans to become net zero by 2060 and is also looking to the construction sector to deliver on this goal. Beijing’s current five-year plan for the energy efficiency of buildings envisages, among other things, retrofitting more than 350 million square meters of buildings to render them energy efficient.
External thermal insulation composite systems are just one lever for promoting sustainability in construction. Are there other options for WACKER POLYMERS to take action here?
In fact, our polymer binders also have a positive effect in other construction applications when it comes to resource conservation and energy efficiency. Take tile mortars, for example. If the traditional thick-bed method is used, the craftsman needs about 14 kilograms of sand and cement to tile a wall or floor area of one square meter. If he uses so-called thin-bed mortar modified with our VAE polymers, only 4.5 kilograms of sand and cement are required, in other words, around two thirds less material. And because the production of cement is known to be very energy-intensive, carbon dioxide emissions are also reduced with the thin-bed method – by around 60 percent, according to our calculations.
So why hasn’t the thin-bed method using polymer-modified tile adhesives long become the norm?
This is in fact the case in developed industrialized nations, especially since it allows the craftsman to install the tiles much faster. In emerging nations, we still see great potential for working in a more resource-conserving, energy-efficient and productive way. Incidentally, one aspect of modern, polymer-modified dry mortar systems that is generally underestimated, is construction site logistics. If building materials in systems such as thin-bed mortar or pumpable self-leveling flooring compounds do not have to be mixed on site, logistics can be significantly reduced. This means: less truck driving, lower CO2 emissions. And of course, work on the construction site becomes more efficient.
Not only that, but sand suitable for cementitious applications such as concrete or mortar is becoming increasingly scarce. This sounds paradoxical at first, because in desert regions it is available like the proverbial sand on the seashore ...
In fact, desert sand is too fine-grained and also too round in structure to be used as an additive in building materials – these grains of sand have been worn smooth by winds over millennia. This is a problem because sand is the largest traded solid resource in the world: humanity consumes 50 billion tons of it annually.
Does WACKER POLYMERS also have a solution for helping to conserve resources in sand?
Yes, we have found a way to replace silica sand in dry mortars, and especially in tile mortars, with recycled concrete if these mortars are modified with our VAE-based binders. Typically, the proportion of quartz sand in the finished tile adhesive is 50 to 60 percent by weight.
Up to half of this additive can be replaced by fine-grain recycled concrete without adversely affecting the properties of the tile adhesive. This conserves natural resources.
External Thermal Insulation Composite Systems in hot Climates – Model House Study in Dubai.
WACKER conducted a joint model house study in cooperation with the state central laboratory in Dubai to investigate the usefulness of thermal insulation even in hot climates.
For this purpose, two identical residential units were constructed and measurements were taken over a period of twelve months. One house was uninsulated, while the other was insulated with an external thermal insulation composite system.
Result: The air-conditioning-related energy consumption and the CO2 emissions of the insulated model house are around 60 percent lower.

Energy losses of a typical unrenovated single-family home without thermal insulation. Up to two-thirds of heating energy is lost through walls and windows, which can be avoided through energy-efficient refurbishment.
Roof: 15%
Window: 25%
Window section: 10%
Wall: 40%
Basement: 10%
Source: EAE – European Association for External Thermal Insulation Composite Systems/Dena

