LIBATEC®: WACKER Launches New Brand for Production Technology for Live Microbial Products (LMPs)
Munich / Amsterdam, Mar 03, 2020
Wacker Biotech is now marketing its technology platform for developing and manufacturing Live Microbial Products (LMPs) under the brand name LIBATEC®. LMPs are a promising class of therapeutic products that open the door to new medical treatments. The WACKER Group is bundling its biopharmaceutical activities within Wacker Biotech, a CDMO (contract development and manufacturing organization) notable for its innovative technologies. LIBATEC® is one of these.
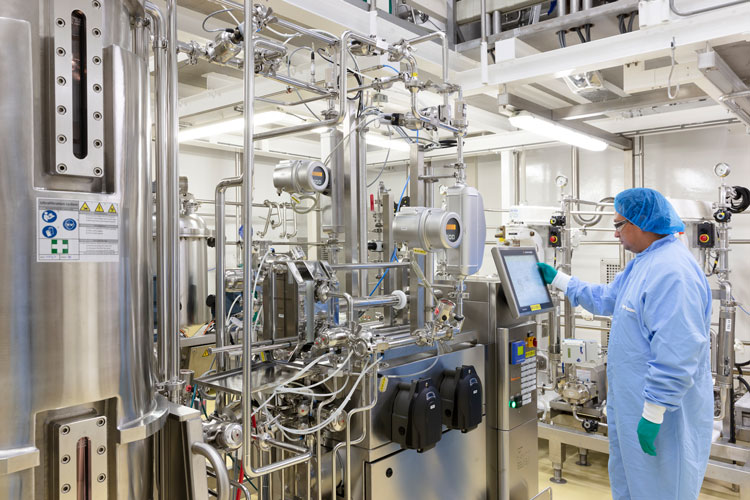
More and more companies are developing what are referred to as Live Microbial Products – pharmaceuticals that contain living microorganisms. The purpose of these actives is to cure or prevent a wide variety of diseases, including infectious diseases, cancer, inflammatory diseases, metabolic diseases, dermatological diseases and many others. Clinical trials potentially leading to market approval are currently underway for a large number of these LMPs. The assumption underlying one scientific study is that the market for human microbiome therapeutics will grow by 33 percent annually in the coming years. “What we have here is a new generation of medications on their way from the laboratory to a clinical setting. That will generate major growth opportunities for us as a microbial contract manufacturer and for our customers,” says Dr. Susanne Leonhartsberger, the managing director of Wacker Biotech GmbH. Development and production of LMPs at Wacker Biotech are based on an efficient, comprehensive production platform now being launched under the brand name LIBATEC®.
Pioneers in LMP Production
Wacker Biotech is a pioneer in the field of LMP production, having begun LMP contract manufacturing at its Amsterdam site in 2006. As a CDMO, the company offers its customers production processes that comply with GMP (good manufacturing practice) standards and are tailored to the needs of the project and development phase at hand. The company manages fermentation regimes for aerobic and certain anaerobic organisms. The Amsterdam site has several production lines that are available for this and that have been approved by the FDA (the US Food and Drug Administration) and the EMA (European Medicines Agency). These lines utilize both single-use bioreactors as well as stainless steel bioreactors up to 1,500 liters. In addition to process development and manufacturing, Wacker Biotech scientists also develop suitable analytical methods for release testing, both within the manufacturing process and for the finished product.
The first step in manufacturing LMPs is to grow bacteria in a culture medium in small bioreactors. This is followed by fermentation in larger reactors, during which the actual production of microorganisms takes place. In a multi-stage process, the organisms obtained are subsequently separated from undesirable constituents, purified and concentrated. One of the many challenges in the LMP production process is that sterile filtration is not an option, since LMPs consist of living microorganisms, which would not survive the process. Specialized analytical tests are needed to ensure an adequate number of living microorganisms in the finished product. The final steps involve converting the finished LMP to a stable form, dispensing it, packaging it and preparing it for transport. A fill-and-finish plant, including freeze-drying equipment (lyophilization), is available for this purpose at the Amsterdam site. “That allows us to offer a closed production system – a deciding factor in meeting the quality requirements both of regulatory agencies and of our customers,” Leonhartsberger points out. Key benefits of LIBATEC® include fermentation regimes for aerobic and certain anaerobic organisms, closed production setups for GMP-compliant, monoseptic processing of up to 1,500 liters and seamless filling/lyophilization capabilities.
Lactococci That Heal Chronic Wounds
An example of a successful partnership: Aurealis Therapeutics AG has been a Wacker Biotech customer since 2016. The company had been searching for a partner to help with process/method development and GMP production of an active agent for chronic wound applications. At Wacker Biotech, the production of the active ingredient was implemented in a fermenter with a capacity of 250 liters. The genetically engineered lactic acid bacteria are intended to promote tissue regeneration in patients with chronic wounds that will not heal. “We are very pleased with the high technical competence, reliability and support of the Wacker team to bring our lead candidate into the clinic as planned - Wacker is a true partner in this project,” notes Juha Yrjänheikki, CEO of Aurealis Therapeutics. The candidate is currently in clinical phase I – also thanks to Wacker Biotech.
About Wacker Biotech
Wacker Biotech GmbH and Wacker Biotech B.V. are full-service contract manufacturers of therapeutic proteins, LMPs and vaccines based on microbial systems. The companies’ portfolios range from strain/process development to analytical testing and GMP-compliant production for clinical as well as commercial supply. Wacker Biotech maintains three GMP-compliant, FDA- and EMA-certified production plants in Amsterdam and in the German cities of Jena and Halle. Wacker Biotech GmbH and Wacker Biotech B.V. are wholly owned subsidiaries of the Munich-based WACKER Group.
For further details, please visit the following website: www.wacker.com/biologics
Or read the feature “Therapeutic Bacteria“ to learn more about Wacker Biotech's business: www.wacker.com/featureservice
Contact

Wacker Chemie AG
Media Relations
Manuela Dollinger
Tel. +49 89 6279-1629
Send message
Download
Press Information
(PDF | 244 KB)