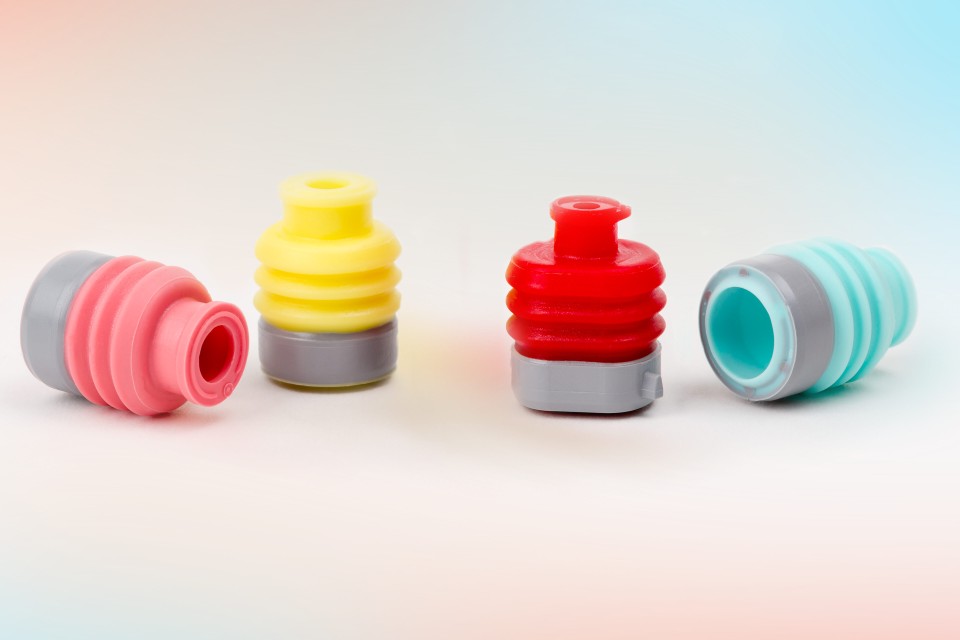
Selective combination of different materials give designers more freedom
Oct 01, 2019 Read time: approx. MinutesMinute
Self-adhesive yet low-friction
WACKER has developed new grades of liquid silicone rubber that adhere well and yet have a low-friction surface immediately after curing – without bleeding any oil. The development opens the door to hard/soft combinations that are easy to process.
Composite parts have become significantly more important over the past twenty years. Reasons for this include growing cost pressures and new requirements for component quality, function and design. Selectively combining different materials to form a composite allows manufacturers to integrate multiple functionalities in a single part while giving designers more freedom. One widely used type of composite combines a soft, elastic component with a hard component that strengthens the composite and lends it its shape. Metal is frequently used as the hard component, although suitable thermoplastic materials are becoming increasingly common as well.
In hard/soft combinations like these, the soft component forms a seal or absorbs vibrations or sound. “More and more manufacturers are choosing silicone elastomers, especially if the final part will be used under harsh conditions, in medical devices, or in contact with food or medicines,” says Dagmar Rische, a marketing manager for Rubber Solutions at WACKER SILICONES. This is where the property profile of silicone elastomers comes into play: silicones are chemically inert, biocompatible, heat-resistant, flexible at low temperatures, resistant to aging and remain elastic for long periods.
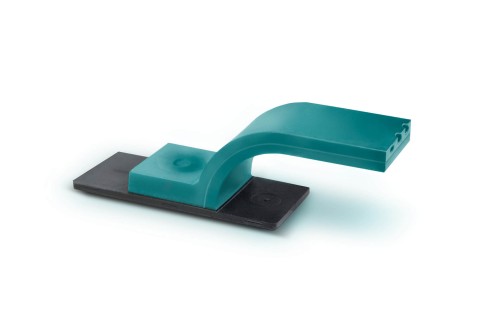
The ISO 813 adhesion test was conducted to demonstrate the adhesive properties of new self-adhesive liquid silicone rubber grades that crosslink to form an intrinsically low-friction surface. The silicone components (turquoise) adhere firmly to the thermoplastic hard components (black), even though the thermoplastic substrate was not treated ahead of time. This opens up the possibility of using two-part injection molding for cost-effective mass production of multicomponent parts made of thermoplastic and silicone elastomer components.
Unless they are specially modified, however, silicone elastomers adhere poorly to other materials, which makes stable multicomponent parts difficult to produce. “In order for conventional silicone elastomers to achieve good adhesion, you have to pretreat the surface of the hard component extensively,” she emphasizes. “For parts manufacturers, that means an additional step.”
A number of applications are negatively impacted by yet another characteristic of silicone elastomers: their typically rubber-like surface, which generates a great deal of frictional resistance. That property can make processing difficult and cause problems in practical applications whenever the final product needs to move along another hard surface.
WACKER solved the first problem – poor adhesive properties – back in 1999 with a patented self-adhesion technology that produces a permanent chemical bond between the two components. Since that time, the availability of specially modified liquid silicone rubber products – self-adhesive grades – has eliminated the need for pretreating hard components. The technology opens the door to using the 2K injection process as a fast, cost-effective method for mass-producing multicomponent parts consisting of silicone elastomers and either a thermoplastic material or metal.
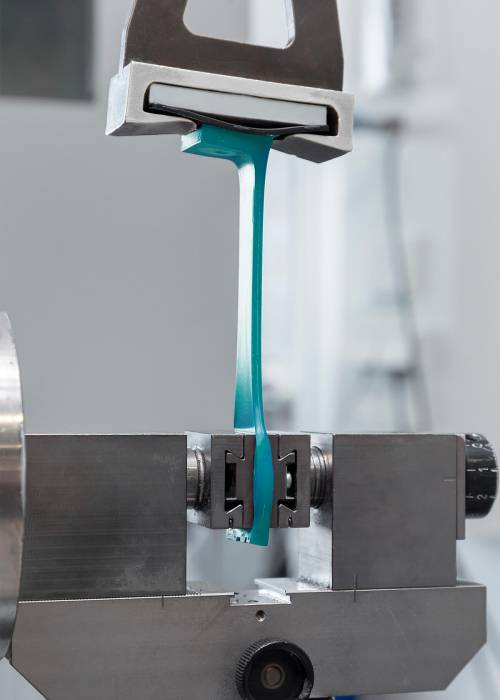
This equipment is used in the applications laboratory to perform the adhesion test on a test piece.
Intrinsic property
In 2007, WACKER presented a solution to the second problem, i.e. the dull surface: a patented technology that creates a low-friction surface on silicone elastomers immediately after they cure – without releasing a lubricating oil as had been the case up to that time. “In silicone products that use this technology, the capacity to reduce friction is an intrinsic property of the material,” stresses Dr. Christof Wörner, who heads an applications laboratory at WACKER SILICONES.
His team of developers has now successfully combined both technologies. The result is a portfolio of liquid silicone rubber grades that are not only self-adhesive – they also yield elastomers with a low-friction yet dry surface. The portfolio includes the ELASTOSIL® LR 3671 and LR 3675 product lines, as well as the SILPURAN® 6760/50 grade.
The friction typically produced by silicones makes silicone products more difficult to work with during assembly and use – it takes considerable effort, for example, to thread silicone tubing through sleeves. One way of resolving the issue of surface friction is through the use of silicone elastomers that bleed oil. These materials contain a special silicone fluid that continuously migrates to the surface of the cured material to produce an oily liquid film, which, in turn, generates the desired low-friction effect.
Oil-bleeding silicone elastomers could be implemented in any applications where the oil discharge is not a problem. Weather packs and sealing mats made of self-lubricating silicones like these have been used in automotive electronics for years, for example. In addition to making the seals easier to install, the exuded oil also offers additional protection from moisture penetration. The oil and dust that stick to the oil film are generally not a concern under the hood.
“Our unique formulation concept allows us to tailor grades specifically for sensitive applications.”
Dr. Christian Wörner, Technical Marketing, Rubber Solutions, WACKER SILICONES

Compression set (%) Cured liquid silicone rubber grades from the ELASTOSIL® LR 3675 product line exhibit low compression set and hence considerable elastic recovery with no postcuring.

Less dynamic friction ELASTOSIL® LR 3675/30 and ELASTOSIL® LR 3675/50 exhibit a reduced coefficient of dynamic friction.
Complicated work steps
In applications that require cleanliness, however, this kind of oil film can be a problem. In medical and food technology applications, for instance, the use of oil-bleeding silicones is prohibited entirely. Up until 2007, the only options in these cases were either to accept the high level of frictional resistance or to modify the surface properties with a subsequent treatment, such as the application of a thin coating. But this meant additional work steps that, in some cases, were complicated and time-consuming.
WACKER technology that produces an intrinsically low-friction silicone surface offers an alternative here, as it reduces friction without the formation of a silicone fluid film. The surface of the silicone elastomer remains dry yet low friction, resulting in a material that feels very different from other silicone elastomers.
The reduced friction produced by the surface has a positive effect on the end product, both during assembly and in the final application. The resulting parts are easier to assemble and are also easier to disassemble for purposes such as maintenance or cleaning. The low-friction surface is particularly helpful when installing parts in tight spaces. Because assembly is easier, manufacturers can produce devices more quickly, and, in many instances, even automate the assembly process.
The ability to reduce friction without the use of oil produces another effect that is likewise highly desirable in a range of applications: when two surfaces of a silicone elastomer come into contact, as is the case in valve openings, for example, they often fuse together at high temperatures. The WACKER technology reduces that tendency, allowing slits in metering valves to remain open.
Fast and inexpensive
Up to now, manufacturers had to choose between using either self-adhesive technology or oil-free friction reduction technology. Both have proven their merit in countless applications for many years now – what’s new is their combination. Bringing them together paves the way for fast, cost-effective mass production of multicomponent parts that consist of silicone elastomers combined with either thermoplastics or metal and that have an intrinsically low-friction silicone surface.
The Munich chemical company has conducted extensive tests in its applications labs on the innovative liquid silicone grades that excel in precisely this combination of technologies. The applications engineers working in Dr. Wörner’s lab paid particularly close attention to adhesive properties and surface friction.
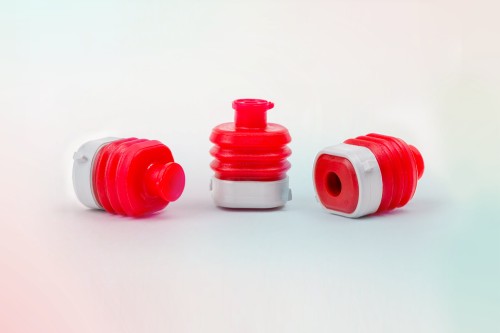
Thanks to their low-friction surface, sealing elements made of ELASTOSIL® LR 3675 make cables easier to assemble in cars. Liquid silicone rubber grades in this product line adhere well to hard components, with no pretreatment required.
No need for priming
The ISO 813 adhesion test demonstrated that the new silicone grades adhere well to a number of thermoplastic materials and metals, with no need for priming or plasma-treating the substrate ahead of time. The materials form a powerful bond on polyamide and polybutylene terephthalate, both of which are frequently used as the hard component in two-part injection molding. Other suitable substrates, however, included polyether ether ketone, polyethylene terephthalate and polymethyl methacrylate. “But processors still always have to test the adhesive properties of their substrates before launching large-scale production,” Wörner advises. That’s because the thermoplastics available on the market may contain additives that affect surface properties and thus adhesion.
The chemical bond generated by WACKER self-adhesive technology offers considerably more design freedom than traditional, mechanical bonding techniques in which the two components of a hard/soft combination are joined through interlocking openings or undercuts. In addition, a chemical bond means that there are no spaces between the hard and soft components where dirt can collect or where bacteria or fungi can become established – an important issue for 2K parts that are used in pharmaceutical or medical devices or that come into contact with food.
All of the grades in this innovative portfolio yield elastomers with lubricating surfaces. Their coefficients of dynamic friction lie between 50 to 70 percent below that of standard self-adhesive silicone elastomers that are equally as hard. The coefficients of friction were measured as directed in EN ISO 8295.
“We applied a unique formulation concept in order to combine the two technologies,” says Wörner. As the WACKER chemist then goes on to explain, “What we did was adapt the formulation components to the applications that the liquid silicone rubber grades had been designed for.” This allowed the developers to do more than simply tailor products for purely technical applications – they were also able to create grades specifically for sensitive applications.
“We applied a unique formulation concept in order to combine the two technologies. What we did was adapt the formulation components to the applications that the liquid silicone rubber grades had been designed for.”
Dr. Christof Wörner, WACKER chemist
SILPURAN® 6760/50 – the medical technology grade
Designed for applications in medical and pharmaceutical technology, WACKER’s self-adhesive, intrinsically lubricating SILPURAN® 6760/50 – the first product in this innovative portfolio to be ready for the market – was unveiled at the COMPAMED 2016 medical technology tradeshow. Following a fine filtration process, WACKER visually inspects this liquid silicone rubber and dispenses it under cleanroom conditions. The product then crosslinks to form an elastomer with a hardness of 50 Shore A.
After postcuring, objects made from SILPURAN® 6760/50 are biocompatible, as demonstrated by select tests meeting ISO 10993 and United States Pharmacopeia (USP) Class V1 standards. The materials were tested according to ISO 10993 with regard to cytotoxicity, pyrogenicity and sensitizing properties. USP Class VI tests included the examination of acute systemic toxicity, intracutaneous toxicity and short-term implantation.
This makes SILPURAN® 6760/50 the silicone soft component of choice for seals used in medical technology or pharmaceutical applications in which a seal moves along another part, as is the case for sealing elements in syringes or piston-type dosing pumps. In both of these cases, the sealing elements are attached to pistons or plungers. During the process of injecting or dispensing a medicine, the seal slides along the inner surface of the syringe and/or pump cylinder.
If the surface of the seal is dull and rubber-like, this movement will be jerky, which can have a negative impact on dosing accuracy and result in pressure surges that feel unpleasant to patients receiving injections or having their blood drawn. If made of SILPURAN® 6760/50, on the other hand, the sealing elements glide uniformly and smoothly along the syringe wall. Plus, the silicone surface does not bleed oil, eliminating the risk of contaminating the medicine.
ELASTOSIL® LR 3671 – compatible with food
ELASTOSIL® LR 3671 was developed especially for food technology applications. This product line includes 30 and 40 Shore A grades, both of which contain only formulation ingredients approved for use in foods. Postcured parts made of ELASTOSIL® LR 3671 are food grade and suitable for contact with food according to the recommendations of Germany’s Federal Institute for Risk Assessment (BfR Recommendation XV Silicones) and the US Food and Drug Administration (21 CFR 177.2600).
Their self-adhesive properties and their intrinsically low coefficients of friction make both grades of ELASTOSIL® LR 3671 suitable for applications in which the silicone components of a multicomponent part move in contact with another surface, either during assembly or in later use. Typical applications here include shaft seals of kitchen appliances, piston seals of dosing pumps and thermos lids with molded-on sealing elements.
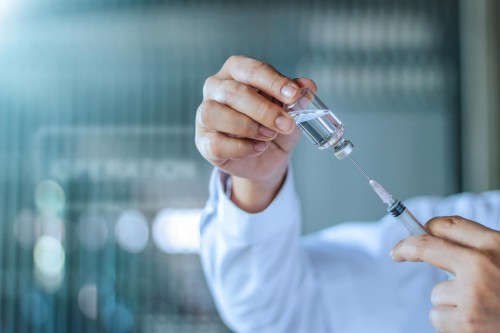
Syringes with a sealing element made of SILPURAN® LR 6760/50 allow medical personnel to inject medications gently and smoothly.
ELASTOSIL® LR 3675 – designed for automotive engineering
The ELASTOSIL® LR 3675 product line likewise includes two grades, in this case with Shore A hardness values of 30 and 50. When developing this product line, WACKER chemists worked with an eye to technical applications, particularly in the automotive sector. The developers turned to an extraordinarily effective adhesion promoter system, to which they then introduced an additive that lends the elastomer a low compression set, even without postcuring. Neither component of the formulation is approved for sensitive applications.
Compression set provides information on the elastic recovery of the elastomer, making it an important parameter for elastomer seals. The ideal value for compression set is 0 percent, which means that the material is perfectly elastic. A completely inelastic material, by contrast, would have a compression set of 100 percent – a seal made of this material would fail.
If the cured rubber is not postcured, the compression set of ELASTOSIL® LR 3675/30 – the 30 Shore A grade – is 14 percent. The compression set of the harder grade (ELASTOSIL® LR 3675/50) is somewhat lower at 12 percent. Those are very good values: testing results for cured, standard self-adhesive silicones of the same hardness and without postcuring are generally much poorer. Sealing elements made of ELASTOSIL® LR 3675, in other words, retain their function for long periods of time. At the same time, these cured silicones also exhibit excellent mechanical properties, even without postcuring. This allows manufacturers of multicomponent parts to eliminate the postcuring step, thus improving productivity.
As with other silicones in this innovative portfolio, ELASTOSIL® LR 3675 likewise forms an intrinsically lubricating surface. For both grades, the coefficient of dynamic friction – measured as described in EN ISO 8295 – is roughly two-thirds lower than standard self-adhesive grades of equal hardness. When cured, ELASTOSIL® LR 3675 naturally exhibits properties typical of silicones, which makes these two grades of liquid silicone rubber the perfect sealing materials for applications under the hood, such as automotive electrical systems.
ELASTOSIL® LR 3675 is therefore the material of choice for producing single-wire seals and connector housings with molded-on radial seals – for any area of an application where a lubricating silicone surface is needed but where a film of exuded silicone fluid would be undesirable. Plugs with molded-on ELASTOSIL® LR 3675 sealing elements are easy to connect, and cables readily slide through molded-on single-wire seals. The risk of contaminating other objects with oil during assembly or later use is never an issue.
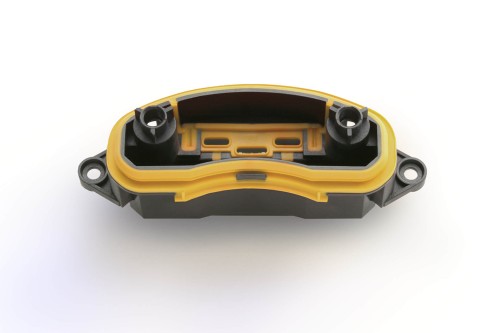
Liquid silicone rubber grades in the ELASTOSIL® LR 3675 product line are perfect for use in automotive electronics, as they adhere well to the thermoplastic polymers used in connector housings – with no pretreatment required.
Silicone elastomers
Silicone elastomers – rubber-elastic solids based on polyorganosiloxanes – are obtained from silicone rubber in a process known as crosslinking or vulcanization. Here, the polymer chains of the organosilicon macromolecules form a three-dimensional network. Silicone elastomers are characterized by a property profile that makes them indispensable in many industrial applications: extraordinary heat resistance, low-temperature flexibility, chemical inertness and biocompatibility. Silicone elastomers possess a highly hydrophobic (i.e. water-repellent) surface, are selectively permeable to gases, and are very good electrical insulators. A typical characteristic is their high resistance to a large number of physical and chemical influences, which is why, unlike organic rubber compounds, they do not age. As a result, their chemical, physical and technical properties remain virtually constant between around −50 and +200 °C; they can also withstand long-lasting mechanical and electrical loads and continued exposure to oxygen, ozone and UV radiation.
Postcuring
In the materials sciences, the term “postcuring” generally refers to a heat treatment that provides a material with its end properties. This also applies to silicones. Postcured silicone parts are superior to their nonpostcured counterparts, both in terms of their engineering properties and biocompatibility. In the case of cured products of addition-curing silicone rubber compounds – a category that includes liquid silicone rubber – postcuring degrades excess crosslinker, improves filler bonding and drives out lowmolecular-weight silicone components. This results in a modest increase in hardness, a significant improvement in tear strength, low compression set and a reduction in the content of volatiles. The established standard method is to postcure silicone pieces at 200 °C in an oven especially designed for this purpose. For safety reasons, the rate of air flow is held continuously high. Since the entire volume of air that flows through the oven has to be heated to 200 °C, postcuring consumes a great deal of energy.
Compression set
If deformed over a long period of time, an elastomer seal will no longer return to its exact shape after release, instead remaining more or less deformed. The extent of this sustained deformity depends on how greatly the elastic recovery of the material decreases under the prevailing storage conditions – deforming forces, the medium that is impacting the material, and the temperature. This information is provided by compression set, a parameter that is determined in a standardized testing procedure. To determine the compression set, an elastomer test specimen (whose shape and dimensions are defined in testing standards) is placed in a compression mechanism, where it is compressed to a previously defined extent and stored in this state for a specific period of time under the testing conditions. Once the test specimen is released, it will no longer return to its original thickness. The thickness of the test specimen is measured before and after compression as well as after relaxation. Expressed as a percentage, the compression set is the ratio of the reduction in thickness following relaxation to the thickness to which the test specimen was compressed. A low compression set is favorable – this shows that the material has high elastic recovery.
Contact
For more information on this topic, please contact:
Mrs. Dagmar Rische
Marketing Manager
Rubber SolutionsWACKER SILICONES
+49 89 6279-1332
dagmar.rische@wacker.com