
Degradable Polymers
Oct 07, 2022 Read time: approx. MinutesMinute
Biopolyesters: Blends with a Boost
VINNEX® polyvinyl acetate-based additives make biodegradable plastics easier to process and improve their material properties – especially when used in combination with silicone-based additives. Four VINNEX® grades are now available as resource-efficient eco products.

Because it is extremely permeable to water vapor and highly transparent, a film made from polylactic acid (PLA) and VINNEX® is ideal for packaging items such as fresh vegetables.
Products made from disposable plastics – including plastic cutlery, drinking straws, stirrers, carry-out containers and to-go cups that would previously have been thrown away after use – have been banned within European Union territory since July 2021. Government efforts to reduce the volumes of plastic waste accumulating around the world have gone hand in hand with increased interest in degradable plastics. The European Bioplastics industry association expects a marked growth in global production capacities for polymers like these, especially biodegradable polyesters, over the next years.
“Unfortunately, potential applications for these plastics are limited at this point. They often lack the property profile that compounders, plastics processors and end users expect from traditional thermoplastics,” explains Dr. Ingo Jeschke, WACKER POLYMERS’ senior business development manager for Resins. They’re difficult to process too. “Both of those weaknesses need to be offset during the compounding process,” Jeschke stresses.
Polymeric organic additives based on polyvinyl acetate have a proven track record when it comes to modifying biodegradable polyesters. Available commercially under the brand name VINNEX®, these products include homo-, co- and terpolymers which, being chemically polar, are perfectly compatible with biopolyesters and starches.
38.3%
Percentage which the melt volume-flow rate – an indicator of workability – of filled polybutylene succinate (PBS) increases when 10 percent VINNEX® 2504 and 1 percent GENIOPLAST® Pellet S are added to the formulation.
“Our VINNEX® additives make biodegradable polymers easier to process, improve their material properties and enhance their compatibility,” says Dominique Nely, head of the Resins global business team at WACKER POLYMERS. This opens up the door to manufacturing compounds from a variety of biopolyesters and starches – in combination with fillers as well.
The VINNEX® portfolio is divided into polymer powders and polymer resins. Because powder grades regulate the crystallization behavior of semi-crystalline biopolyesters, they ensure that the end properties are stable over time, while also improving the impact strength and flexibility of the biopolyester. The primary role of VINNEX® resins is to serve as a processing aid, Enhancing, e.g., the melt strength of the biopolyester to make it easier to handle.
WACKER will be at the K 2022 Trade Fair for Plastics and Rubber, where it will present four additives from its VINNEX® product portfolio that are made from polyvinyl acetate using resource-efficient manufacturing methods: VINNEX® eco 2522, VINNEX® eco 2525, VINNEX® eco 2504 and VINNEX® eco 2505. The VINNEX® eco product line is manufactured from renewable resources based on the mass balance approach, in which both fossil and renewable raw materials are introduced at the beginning of the production cycle. The mass balance approach is then used to mathematically determine the percentage of solid resins made from renewable raw materials. VINNEX® eco products possess the same chemical and physical properties as the standard products, but they have a lower carbon footprint. All VINNEX® eco products are certified in accordance with the REDcert² certification standard.
“Biodegradable polyesters often fail to deliver the property profile that processors and consumers expect.”
Dr. Ingo Jeschke, WACKER POLYMERS
Additives in the VINNEX® or VINNEX® eco product lines can also be combined with silicone-based additives, which WACKER markets under the brand name GENIOPLAST® Pellet. Universally suitable for compounding any type of thermoplastic, GENIOPLAST® Pellet products reduce the effects of friction to make processing easier and improve the end properties of the plastic.
WACKER chemists selected two biodegradable plastics for a screening study on the combined use of VINNEX® and GENIOPLAST® additives: polylactic acid and polybutylene succinate. While these biopolyesters are, in principle, considered alternatives to conventional thermoplastics, they are difficult to process and require suitable additives to achieve the property profile of traditional thermoplastics.
“VINNEX® makes biopolyesters easier to process and improves their material properties.”
Dominique Nely, head of the Resins Global Business Team, WACKER POLYMERS
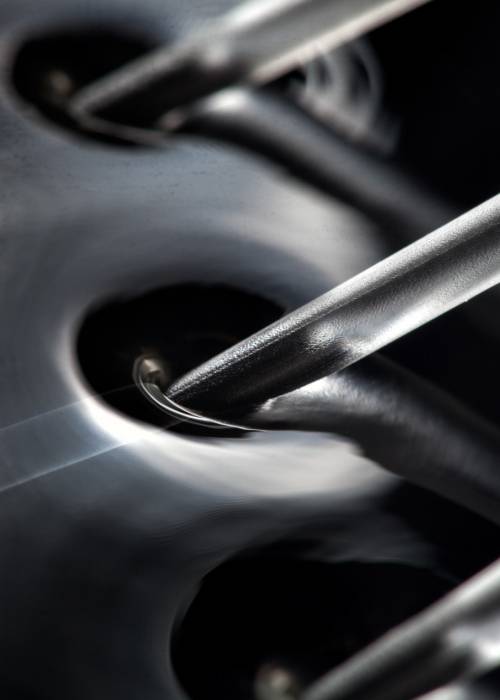
Preliminary stage for the production of blown or cast film: transparent pellet stock is made from a bioplastic and VINNEX® 2526. During this process, the strands pass through a water bath.
More Than the Sum of Its Parts
The key finding of the screening study is the observation that the effects of VINNEX® and GENIOPLAST® complement each other – in both filled and unfilled bioplastic systems. A closer look at the advantages:
— Using VINNEX® and GENIOPLAST® together allows manufacturers to optimize the processing and performance properties of bioplastics to meet specific requirements. The additives are more effective in combination than when used separately.
— Depending on the grade used, VINNEX® has a positive influence either on the behavior of the polymer melt or on the mechanical properties. The additive also ensures that bioplastics can be processed without difficulty.
— When mixed with VINNEX®, GENIOPLAST® primarily improves the surface properties of the plastic product, especially in filled systems.
— In the bioplastic samples that were tested, GENIOPLAST® acts as a booster when added to VINNEX®, enhancing the effects achieved with the latter. In some cases, it also improves properties that are not affected by VINNEX®. For example, the addition of GENIOPLAST® reduces surface friction, thus increasing the bioplastics’ scratch and abrasion resistance. This is verified by examination of the depth and roughness of scratches with a confocal microscope.
— This combination of additives also improves the mechanical properties of the final product: when used together, VINNEX® and GENIOPLAST® make bioplastics more flexible and impact resistant and increase elongation at break in filled systems without sacrificing thermostability. Plastics modified in this way are thus suitable for applications previously reserved for conventional thermoplastics.
— When added in the usual amounts and depending on the individual system, VINNEX® and and GENIOPLAST® additives do not compromise the degradability of thermoplastic starches, of biopolyesters such as polybutylene succinate or polylactic acid or of combinations of these biodegradable polymers.
Mr. Dr. Ingo Jeschke
Senior Business Development Manager
WACKER POLYMERS
+49 8677 83-86906
ingo.jeschke@wacker.com